超硬合金の加工方法
超硬材料 は、超硬合金粉末とコバルト、鉄、ニッケルなどの結合金属などの固体結合材をプレス、焼結などの加工を経て作られる。高硬度(硬度範囲86HRA~94HRA)、高強度、高耐摩耗性などの優れた特性を持ち、従来の切削工具では加工が困難でした。超硬合金の加工方法は?以下の内容を通して、超硬合金の切削加工と超硬合金棒・板の切削方法について詳しく説明します。
I.超硬合金および超硬合金の従来の切断方法
従来の超硬合金の切削方法には、研削、電気スパーク、ワイヤーカットなどがあるが、以下に簡単に紹介する。
1.研削方法。
研削方法は、一般的に使用される超硬合金の切削方法であり、CBN砥石、グリーンカーバイド砥石、ダイヤモンド砥石を使用して切削することができます。超硬合金の靭性、硬度、耐摩耗性に応じて、適切な切削パラメータと研削用工具を選択することで、満足のいく切削結果を得ることができる。しかし、この方法は小面積の切削に適しており、長時間の研削は工具の摩耗や加工効率の低下を招きやすい。
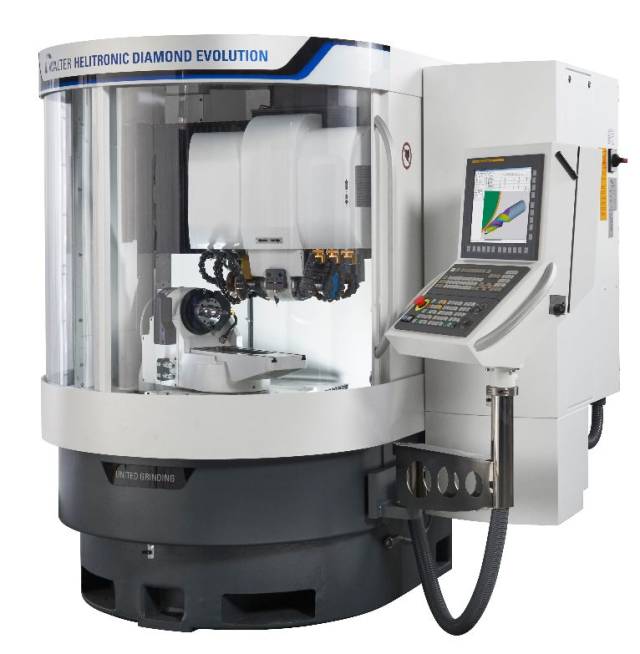
2.超硬合金のエレクトロスパーク加工。
放電加工や電食加工とも呼ばれるエレクトロスパーク加工は、工具電極と被加工物間のパルス放電による電食現象を利用して余分な金属を侵食し、部品のサイズ、形状、表面品質に関する所定の加工要件を達成する。この技術は非接触加工の特徴を持ち、高硬度、高脆性、難削材の複雑な形状や精密な寸法を実現することができる。
(1).高精度加工エレクトロスパーク加工は、ミクロンレベル、あるいはナノレベルの加工精度を達成することができ、超硬合金部品の高精度要求を満たすことができる。
(2).高い表面品質:エレクトロスパーク加工では、工具電極とワークが直接接触しないため、切削力によるワーク表面へのダメージが回避され、より高い表面品質が得られる。
(3).複雑形状の加工エレクトロスパーク加工は、材料の硬度や脆性に制限されず、様々な複雑形状・構造の超硬合金部品の加工が可能です。
エレクトロスパーク加工は、超硬合金加工において多くの利点があるが、いくつかの限界や課題もある。第一に、エレクトロスパーク加工の速度は比較的遅く、加工効率は低い。第二に、放電加工の過程で大量の電気エネルギーと電極材料が消費され、コストがかかる。さらに、放電加工には高い装置精度と安定性が要求され、操作とメンテナンスが難しい。これは、タングステンカーバイドブロックを機械加工するために一般的に使用されます、 EDMブロック 金型産業用。また、タングステンカーバイトロッドをカットします。
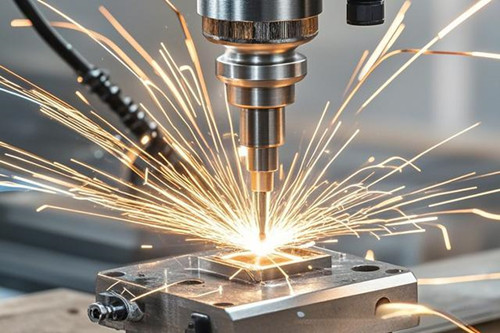
3.超硬合金、タングステンカーバイドのワイヤーカット加工方法。
ワイヤーカットは高速切断技術である。高周波電流によって発生する電気火花によって、直線状の切断ワイヤが鋸歯状に加工物に入り込み、加工物の表面に微小なエッチングを形成する。ワイヤの鋸歯が連続的に除去されるため、大面積の切断が可能になる。しかし、ワイヤーカットには一定の限界がある。例えば、被加工物の厚み、形状、大きさが一定の範囲内にある必要がある。導体としての超硬合金は、ワイヤー切断の要件を満たすことができます。電極線の走行速度によって、放電加工ワイヤ切断機は主に高速ワイヤ放電加工ワイヤ切断機と低速ワイヤ放電加工ワイヤ切断機に分けられる。前者の電極線(モリブデン線)は8~10m/sの高速で往復し、加工速度は速いが、電極線がブレやすく加工品質に影響する。後者の電極線(銅線)は0.2m/s以下の低速で一方向に動く。後者の電極線(銅線)は0.2m/s以下の速度で一方向に移動する。放電後、電極線は使用されなくなり、作業はより安定し、加工品質はより良いが、加工速度は比較的遅い。他の金型材料の加工に比べて、CNCワイヤーカット工作機械での超硬合金の加工生産性は最も低い。厚さが20mm以下の薄いワークの場合、ワイヤーカットは比較的簡単で、表面品質と加工速度は理想的である。厚みが20mmを超えるような厚いワークでは、加工の難易度が上がり、断線や不安定な加工が発生しやすくなる。解決策としては、太い電極線に交換する、より安定した加工液を使用する、工作機械のパラメーターを調整するなどがある。超硬ワイヤーの最大切断長は600mmに達する。超硬合金は、スローワイヤー切断で特に優れた性能を発揮します。スローワイヤー切断は加工精度が高く、表面品質が良いため、複雑な形状や高い精度が要求される超硬部品の加工に特に適しています。超硬合金は硬度が高く、耐摩耗性に優れているため、スローワイヤー切断は電極線の損失を効果的に回避することができ、電極線の寿命を延ばし、加工効率を向上させることができます。多くの工場がこの方法で タングステンカーバイトロッド.
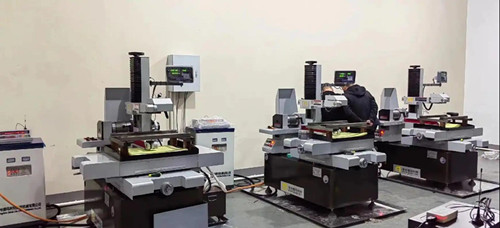
II.レーザー切断方法 ウォルフラムカーバイド および超硬合金
レーザー切断は、近年急速に出現し、発展してきた新しいタイプの超硬合金切断方法であり、高効率、高精度、自動化の利点があります。超硬合金を切断する場合、レーザー切断は切り込み幅を0.2mm以下にすることができ、切断速度が速く、切断品質と効率に明らかな利点があります。
しかし、レーザー切断にはいくつかの問題もある。例えば、切断工程で発生する高温は、材料の変形や損傷、欠陥を引き起こしやすい。同時に、レーザー切断装置の価格は比較的高く、大量生産には適していない。
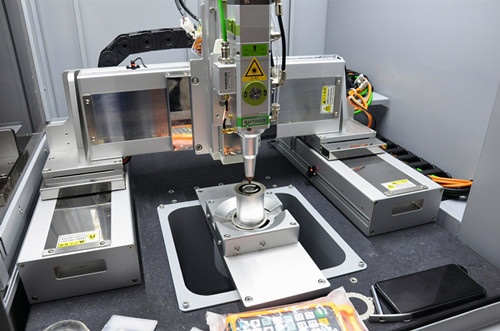
III.超硬合金および超硬合金の超音波切断法。
超音波加工は高周波振動によって加工され、その周波数は通常20kHz以上である。加工中、超音波によって発生する音波が加工工具を超高速で振動させることで、微細レベルでの高速切削、摩擦、研削、欠損を発生させ、被加工物の加工を実現する。超音波加工は、高能率、高精度、高仕上げ面精度が得られ、難加工材にも適しているため、超硬材料の切削加工に広く利用されている。
超硬合金の超音波切断の原理と利点:
超音波加工 高周波振動をカットし、次のような利点がある:
高効率:超音波振動は高速で、作用面積が小さいので、被加工物を非常に短時間で加工できる。
高精度:振動が非常に小さいため、非常に高い加工精度が得られる。
高い表面仕上げ:作用面積が小さいため、表面仕上げが高く、その後の加工工程を減らすことができる。
難加工材にも対応超音波加工は大きな熱を発生させる必要がないため、難加工材を比較的短時間で加工できる。
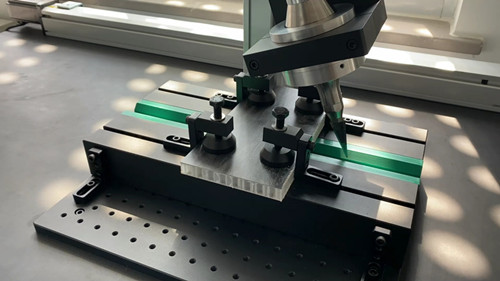
IV.まとめ
超硬合金の加工方法は?超硬合金の切断方法には、それぞれ長所と短所、適用範囲があります。従来の切断方法は、小面積の切断や小ロット加工に適しており、レーザー切断方法は、大面積の切断や高能率・高精度加工に適しています。したがって、さまざまな加工要件や材料特性に応じて適切な切断方法を選択することが極めて重要である。