Wie bearbeitet man Wolframkarbid?
Werkstoffe aus Sinterkarbid werden aus Metallpulver Wolframkarbidpulver und festen Bindemitteln wie Bindemetallen wie Kobalt, Eisen, Nickel usw. durch Pressen, Sintern und andere Verfahren hergestellt. Sie haben eine hohe Härte (Härtebereich 86HRA-94HRA), hohe Festigkeit, hohe Verschleißfestigkeit und andere hervorragende Eigenschaften, so dass sie mit herkömmlichen Schneidwerkzeugen nur schwer zu bearbeiten sind. Wie wird Wolframkarbid bearbeitet? Ich werde das Schneiden von Hartmetall und die Schneidmethoden von Hartmetallstäben und -platten im Detail durch den folgenden Inhalt erklären.
I. Traditionelle Schneidverfahren zum Schneiden von Hartmetall und Sinterkarbid
Zu den traditionellen Hartmetallschneidverfahren gehören Schleifen, Funkenschlag, Drahtschneiden und andere Verfahren, die im Folgenden kurz vorgestellt werden.
1. Verfahren zum Schleifen.
Das Schleifen ist eine gängige Methode zum Schneiden von Hartmetall, das mit CBN-Schleifscheiben, grünen Siliziumkarbid-Schleifscheiben und Diamantschleifscheiben bearbeitet werden kann. Je nach Zähigkeit, Härte und Verschleißfestigkeit des Hartmetalls können durch die Auswahl geeigneter Schneidparameter und Schleifwerkzeuge zufriedenstellende Schneidergebnisse erzielt werden. Diese Methode eignet sich jedoch nur für das Schneiden kleiner Flächen, und bei längerem Schleifen kann es leicht zu Werkzeugverschleiß und geringer Bearbeitungseffizienz kommen.
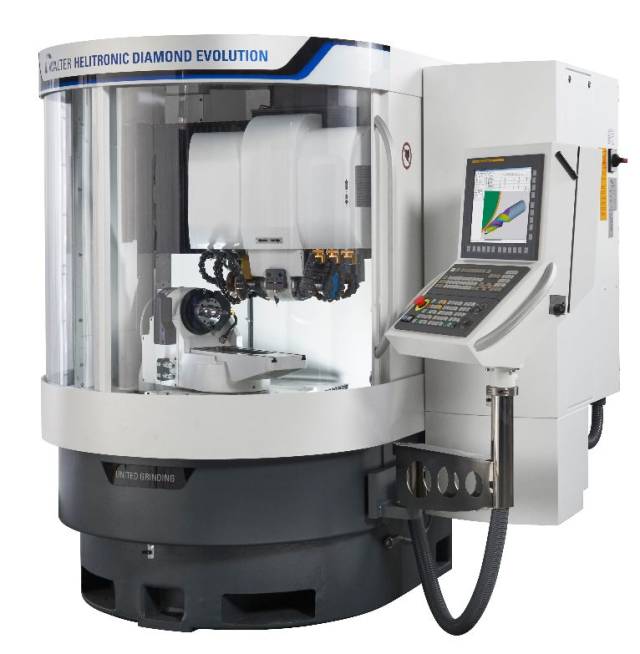
2. Elektrospark-Bearbeitung von Wolframkarbid.
Bei der elektroerosiven Bearbeitung, die auch als Entladungsbearbeitung oder Elektroerosionsbearbeitung bezeichnet wird, wird das Elektrokorrosionsphänomen der Impulsentladung zwischen der Werkzeugelektrode und dem Werkstück genutzt, um überschüssiges Metall abzutragen und so die vorgegebenen Bearbeitungsanforderungen in Bezug auf Größe, Form und Oberflächenqualität der Teile zu erfüllen. Diese Technologie hat die Eigenschaften einer berührungslosen Bearbeitung und kann komplexe Formen und Präzisionsmaße bei hochharten, hochspröden und schwer zu bearbeitenden Werkstoffen erzielen.
(1). Hochpräzise Bearbeitung: Mit der Elektrofunkenbearbeitung kann eine Bearbeitungsgenauigkeit im Mikrometer- oder sogar Nanobereich erreicht werden, die den hohen Präzisionsanforderungen von Hartmetallteilen gerecht wird.
(2). Hohe Oberflächenqualität: Während der Funkenerosion gibt es keinen direkten Kontakt zwischen der Werkzeugelektrode und dem Werkstück, wodurch die Beschädigung der Werkstückoberfläche durch die Schnittkraft vermieden wird, so dass eine höhere Oberflächenqualität erzielt werden kann.
(3). Bearbeitung komplexer Formen: Die elektrofunkengestützte Bearbeitung ist nicht durch die Härte und Sprödigkeit des Werkstoffs begrenzt und kann Hartmetallteile mit verschiedenen komplexen Formen und Strukturen bearbeiten.
Obwohl die Funkenerosion bei der Bearbeitung von Hartmetall viele Vorteile hat, gibt es auch einige Einschränkungen und Herausforderungen. Erstens ist die Geschwindigkeit der Funkenerosion relativ langsam und die Effizienz der Bearbeitung ist gering. Zweitens werden beim Funkenerodieren eine große Menge an elektrischer Energie und Elektrodenmaterial verbraucht, was kostspielig ist. Darüber hinaus erfordert das Funkenerodieren eine hohe Genauigkeit und Stabilität der Ausrüstung und ist schwierig zu bedienen und zu warten. Dieses Verfahren wird in der Regel für die Bearbeitung von Hartmetallblöcken verwendet, EDM-Blöcke für die Formenindustrie. Und auch schneiden Wolframkarbidstangen.
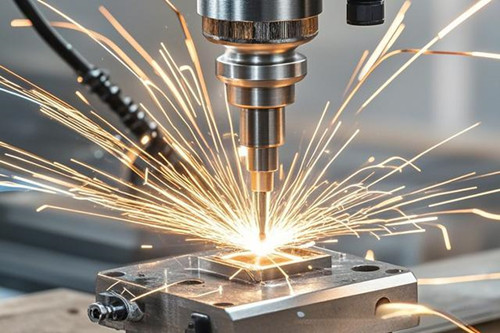
3. Drahtschneideverfahren zur Bearbeitung von Sinterkarbid und Wolframkarbid.
Das Drahtschneiden ist eine Hochgeschwindigkeitsschneidetechnik. Der durch Hochfrequenzstrom erzeugte elektrische Funke bewirkt, dass der lineare Schneiddraht zackenförmig in das Werkstück eindringt und winzige Ätzungen auf der Oberfläche des Werkstücks bildet. Da die Drahtverzahnungen kontinuierlich entfernt werden, kann ein großflächiges Schneiden erreicht werden. Dem Drahtschneiden sind jedoch gewisse Grenzen gesetzt. So müssen beispielsweise Dicke, Form und Größe des Werkstücks innerhalb eines bestimmten Bereichs liegen. Sinterkarbid als Leiter kann die Anforderungen des Drahtschneidens erfüllen. Je nach Laufgeschwindigkeit des Elektrodendrahts werden die Drahterodiermaschinen hauptsächlich in zwei Kategorien unterteilt: Hochgeschwindigkeitsdrahterodiermaschinen und Niedergeschwindigkeitsdrahterodiermaschinen. Der erste Elektrodendraht (Molybdändraht) bewegt sich mit einer hohen Geschwindigkeit von 8-10m/s hin und her, und die Bearbeitungsgeschwindigkeit ist schnell, aber der Elektrodendraht ist leicht zu erschüttern, was die Bearbeitungsqualität beeinträchtigt; der zweite Elektrodendraht (Kupferdraht) bewegt sich unidirektional mit einer Geschwindigkeit von weniger als 0,2m/s. Der Elektrodendraht wird nach der Entladung nicht mehr verwendet, und die Arbeit ist stabiler, die Verarbeitungsqualität ist besser, aber die Verarbeitungsgeschwindigkeit ist relativ langsam. Verglichen mit der Bearbeitung anderer Formwerkstoffe ist die Bearbeitungsproduktivität von Hartmetall auf CNC-Drahtschneidmaschinen am geringsten. Bei dünneren Werkstücken mit einer Dicke von weniger als 20 mm ist das Drahterodieren relativ einfach, und die Oberflächenqualität und Bearbeitungsgeschwindigkeit sind ideal. Bei dickeren Werkstücken mit einer Dicke von mehr als 20 mm nimmt die Schwierigkeit der Bearbeitung zu, und es kann zu Drahtbrüchen und instabiler Bearbeitung kommen. Zu den Lösungen gehören der Austausch dickerer Elektrodendrähte, die Verwendung stabilerer Arbeitsmittel und die Anpassung der Werkzeugmaschinenparameter. Die maximale Länge beim Schneiden von Hartmetalldrähten kann bis zu 600 mm betragen. Sinterkarbid eignet sich besonders gut für das langsame Drahterodieren. Das langsame Drahtschneiden zeichnet sich durch hohe Bearbeitungsgenauigkeit und gute Oberflächenqualität aus und eignet sich besonders für die Bearbeitung von Hartmetallteilen mit komplexen Formen und hohen Präzisionsanforderungen. Aufgrund der hohen Härte und der guten Verschleißfestigkeit von Hartmetallwerkstoffen kann das Langsamdrahtschneiden den Verlust des Elektrodendrahtes wirksam vermeiden, wodurch die Lebensdauer des Elektrodendrahtes verlängert und die Bearbeitungseffizienz verbessert wird. Viele Fabriken verwenden diese Methode zum Schneiden von Wolframkarbid-Stab.
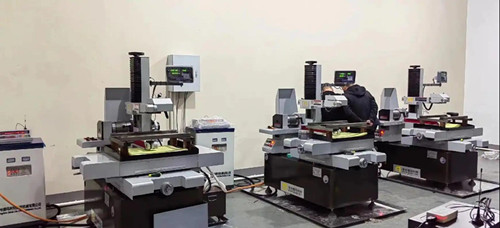
II. Laserschneidverfahren für Maschinen Wolframcarbid und Sinterkarbid
Das Laserschneiden ist eine neue Art des Hartmetallschneidens, die sich in den letzten Jahren rasant entwickelt hat und die sich durch hohe Effizienz, hohe Präzision und Automatisierung auszeichnet. Beim Schneiden von Hartmetall, Laserschneiden kann die Schnittbreite weniger als 0,2 mm, die Schnittgeschwindigkeit ist schnell, und es hat offensichtliche Vorteile in der Schnittqualität und Effizienz.
Allerdings gibt es auch einige Probleme beim Laserschneiden. So kann die hohe Temperatur, die beim Schneiden entsteht, leicht zu Materialverformungen, Schäden und Defekten führen. Gleichzeitig ist der Preis der Laserschneidausrüstung relativ hoch und eignet sich nicht für die Massenproduktion.
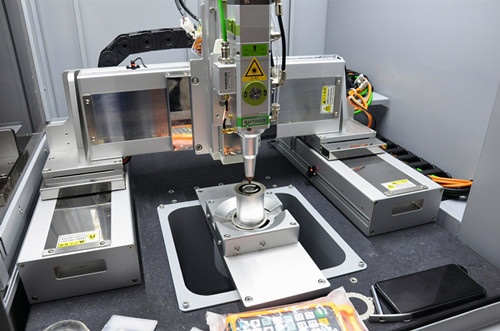
III. Ultraschallschneidverfahren für die Bearbeitung von Wolframkarbid und Hartmetall.
Die Ultraschallbearbeitung erfolgt durch hochfrequente Schwingungen, deren Frequenz in der Regel über 20 kHz liegt. Während des Bearbeitungsprozesses lassen die durch Ultraschall erzeugten Schallwellen das Bearbeitungswerkzeug mit extrem hoher Geschwindigkeit vibrieren, wodurch Hochgeschwindigkeitsschneiden, Reibung, Schleifen und Verlust auf mikroskopischer Ebene erzeugt werden, um die Bearbeitung des Werkstücks zu erreichen. Die Ultraschallbearbeitung wird wegen ihrer hohen Effizienz, hohen Präzision, hohen Oberflächengüte und ihrer Eignung für schwer zu bearbeitende Werkstoffe häufig für das Schneiden von Hartmetall eingesetzt.
Grundsätze und Vorteile des Ultraschallschneidens von Hartmetall:
Bearbeitung mit Ultraschall durchdringt hochfrequente Schwingungen und hat folgende Vorteile:
Hohe Effizienz: Die Ultraschallschwingung ist sehr schnell und hat einen kleinen Aktionsbereich, so dass das Werkstück in sehr kurzer Zeit bearbeitet werden kann.
Hohe Präzision: Da die Vibration sehr gering ist, kann eine sehr hohe Bearbeitungsgenauigkeit erreicht werden.
Hohe Oberflächengüte: Die kleine Aktionsfläche sorgt für eine hohe Oberflächengüte, wodurch die nachfolgenden Bearbeitungsschritte reduziert werden.
Anwendbar auf schwer zu bearbeitende Materialien: Da bei der Ultraschallbearbeitung keine große Wärmemenge erzeugt werden muss, können schwer zu bearbeitende Materialien in relativ kurzer Zeit bearbeitet werden.
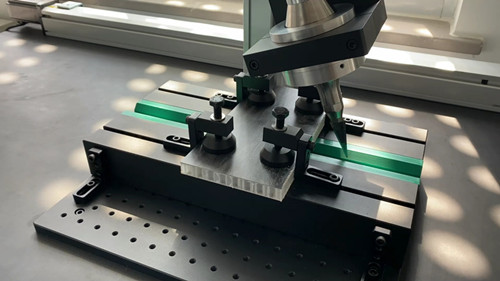
IV. Zusammenfassung
Wie wird Wolframkarbid bearbeitet? Verschiedene Hartmetallschneidverfahren haben ihre Vor- und Nachteile und ihren Anwendungsbereich. Herkömmliche Schneidverfahren eignen sich für das Schneiden von kleinen Flächen und die Bearbeitung von Kleinserien, während Laserschneidverfahren eher für großflächiges Schneiden, hohe Effizienz und hochpräzise Bearbeitung geeignet sind. Daher ist es von entscheidender Bedeutung, das richtige Schneidverfahren je nach den unterschiedlichen Bearbeitungsanforderungen und Materialeigenschaften zu wählen.