Wie man Wolframkarbid auf Stahl schweißt
1. die Eigenschaft des Lötschweißens:
Werkzeugstahl umfasst in der Regel Kohlenstoff-Werkzeugstahl, legierten Werkzeugstahl und Schnellarbeitsstahl, während Sinterkarbid durch Sintern von Karbiden (wie Wolframcarbid, TiC, etc.) und Bindemetalle (wie Co, etc.) durch Pulver. Die Technologie des Hartlötschweißens von Werkzeugstahl und Sinterkarbid oder Hartmetallbuchsen wird hauptsächlich für die Herstellung von Schneidewerkzeuge, Schimmelpilze, Messgeräte und Bergbauwerkzeuge. In diesem Artikel wird das Schweißen von Wolframkarbid oder Hartmetall im Detail vorgestellt.
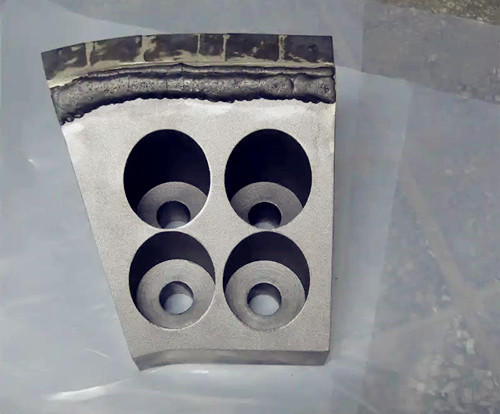
Das Hauptproblem beim Hartlöten von Werkzeugstahl besteht darin, dass seine Struktur und Leistung durch den Lötprozess leicht beeinträchtigt werden. Wenn der Lötprozess unsachgemäß ist, kann es sehr leicht zu Problemen wie Hochtemperaturglühen, Oxidation und Entkohlung kommen. Die Abschrecktemperatur von Schnellarbeitsstahl W18Cr4V beträgt beispielsweise 1260-1280 °C. Um die oben genannten Probleme zu vermeiden und die maximale Härte und Verschleißfestigkeit beim Schneiden zu gewährleisten, muss die Löttemperatur an die Abschrecktemperatur angepasst werden.
Die Löteigenschaften von Sinterkarbid sind schlecht. Das liegt daran, dass der Kohlenstoffgehalt von Sinterkarbid hoch ist und die ungereinigte Oberfläche oft mehr freien Kohlenstoff enthält, der die Benetzung des Hartlotes behindert. Darüber hinaus wird Sinterkarbid bei der Löttemperatur leicht oxidiert und bildet einen Oxidfilm, der ebenfalls die Benetzung des Hartlots beeinträchtigt. Daher ist die Oberflächenreinigung vor dem Hartlöten sehr wichtig, um die Benetzbarkeit des Hartlots auf Sinterkarbid zu verbessern. Falls erforderlich, können auch Maßnahmen wie Oberflächenverkupferung oder Vernickelung ergriffen werden.
Ein weiteres Problem beim Hartlöten oder Schweißen mit Wolframkarbid ist die Rissbildung in der Verbindung. Das liegt daran, dass der lineare Ausdehnungskoeffizient nur halb so groß ist wie der von Stahl mit niedrigem Kohlenstoffgehalt. Wenn Sinterkarbid mit dem Substrat eines solchen Stahls verlötet wird, entsteht in der Verbindung eine große thermische Spannung, die zu Rissen führt. Daher sollten beim Hartlöten von Sinterkarbid mit anderen Werkstoffen Maßnahmen zur Vermeidung von Rissen getroffen werden.
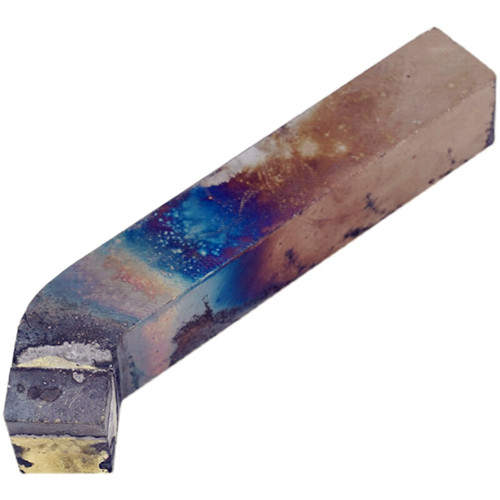
2. die Materialien für das Hartlöten:
(1) Hartlot Reine Kupfer-, Kupfer-Zink- und Silber-Kupfer-Hartlote werden normalerweise zum Hartlöten von Werkzeugstahl und Hartmetall verwendet. Reines Kupfer hat eine gute Benetzbarkeit für verschiedene Hartmetalle, aber es muss in einer wasserstoffreduzierenden Atmosphäre gelötet werden, um die beste Wirkung zu erzielen. Gleichzeitig ist aufgrund der hohen Löttemperatur die Spannung in der Verbindung groß, was zu einer erhöhten Rissneigung führt. Die Scherfestigkeit der mit reinem Kupfer gelöteten Verbindung beträgt etwa 150 MPa, und die Plastizität der Verbindung ist ebenfalls hoch, aber sie ist nicht für Hochtemperaturarbeiten geeignet.
Kupfer-Zink-Hartlot ist das am häufigsten verwendete Hartlot zum Hartlöten von Werkzeugstahl und Sinterkarbid. Um die Benetzbarkeit des Hartlots und die Festigkeit der Verbindung zu verbessern, werden dem Hartlot häufig Legierungselemente wie Mn, Ni und Fe zugesetzt. B-Cu58ZnMn enthält beispielsweise 4% w(Mn), wodurch die Scherfestigkeit der Hartmetall-Lötverbindung bei Raumtemperatur 300-320MPa erreicht: bei 320°C kann sie immer noch 220-240MPa halten. Wenn man B-Cu58ZnMn eine kleine Menge Co hinzufügt, kann die Scherfestigkeit der Lötverbindung 350MPa erreichen, und es hat eine hohe Schlagzähigkeit und Ermüdungsfestigkeit, was die Lebensdauer von Schneidwerkzeugen und Gesteinsbohrwerkzeugen erheblich verbessert.
Das Silber-Kupfer-Lot hat einen niedrigen Schmelzpunkt, und die durch die Lötverbindung erzeugte Wärmespannung ist gering, was dazu beiträgt, die Rissneigung des Hartmetalls während des Lötens zu verringern. Um die Benetzbarkeit des Hartlots zu verbessern und die Festigkeit und Arbeitstemperatur der Verbindung zu erhöhen, werden dem Hartlot häufig Legierungselemente wie Mn und Ni zugesetzt. Das Hartlot B-Ag50CuZnCdNi hat beispielsweise eine ausgezeichnete Benetzbarkeit auf Hartmetall, und die Lötverbindung weist eine gute Gesamtleistung auf.
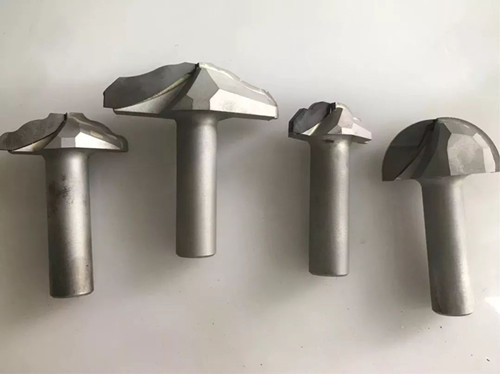
Zusätzlich zu den oben genannten drei Arten von Hartloten können Hartlote auf Mn- und Ni-Basis, wie B-Mn50NiCuCrCo und B-Ni75CrSiB, für Hartmetalle verwendet werden, die bei Temperaturen über 500°C und mit hohen Anforderungen an die Verbindungsfestigkeit eingesetzt werden. Für das Hartlöten von Schnellarbeitsstählen sollte ein spezielles Hartlot mit einer Löttemperatur gewählt werden, die der Abschrecktemperatur entspricht, wie in Tabelle 3 dargestellt; diese Art von Hartlot wird in zwei Kategorien unterteilt. Die eine ist das Ferromangan-Hartlot, das hauptsächlich aus Ferromangan und Borax besteht. Die Scherfestigkeit der Lötverbindung liegt im Allgemeinen bei etwa 100 MPa, aber die Verbindung neigt zu Rissen: die andere ist eine spezielle Kupferlegierung, die Ni, Fe, Mn und Si enthält. Die damit gelötete Verbindung ist rissunempfindlich, und ihre Scherfestigkeit kann auf 300 MPa erhöht werden.
(2) Hartlötflussmittel und Schutzgas Die Wahl des Hartlötflussmittels sollte auf den zu schweißenden Grundwerkstoff und das gewählte Hartlot abgestimmt sein. Beim Löten von Werkzeugstahl und Hartmetall werden hauptsächlich Borax und Borsäure als Flussmittel verwendet, und einige Fluoride (KF, NaF, CaF2, usw.) zugesetzt werden. Kupfer-Zink-Hartlote werden mit den Flussmitteln FB301, FB302 und FBl05 und Silber-Kupfer-Hartlote mit den Flussmitteln FBl01~FBl04 versehen. Beim Löten von Schnellarbeitsstahl mit speziellen Hartloten wird hauptsächlich das Flussmittel Borax verwendet.
Um die Oxidation des Werkzeugstahls während des Erhitzens des Lotes zu verhindern und die Reinigung nach dem Löten zu vermeiden, kann das Löten unter Schutzgas erfolgen. Das Schutzgas kann ein Inertgas oder ein reduzierendes Gas sein, und der Taupunkt des Gases muss unter -40°C liegen. Sinterkarbid kann unter Wasserstoffschutz gelötet werden, und der Taupunkt des erforderlichen Wasserstoffs sollte unter -59°C liegen.
3. die Löttechnik:
Werkzeugstahl muss vor dem Löten gereinigt werden, und die bearbeitete Oberfläche darf nicht zu glatt sein, um das Benetzen und Verteilen des Hartlotes und des Lotes zu erleichtern. Die Oberfläche von Sinterkarbid sollte vor dem Löten mit Siliziumkarbid oder einer Diamantschleifscheibe sandgestrahlt oder poliert werden, um überschüssigen Kohlenstoff auf der Oberfläche zu entfernen, damit sie während des Lötens vom Hartlot benetzt werden kann. Sinterkarbid, das Titankarbid enthält, ist schwieriger zu benetzen. Durch Auftragen von Kupfer- oder Nickeloxidpaste auf die Oberfläche und Einbrennen in einer reduzierenden Atmosphäre, um den Übergang von Kupfer oder Nickel an die Oberfläche zu bewirken, wird die Benetzbarkeit des Hartlots verbessert.
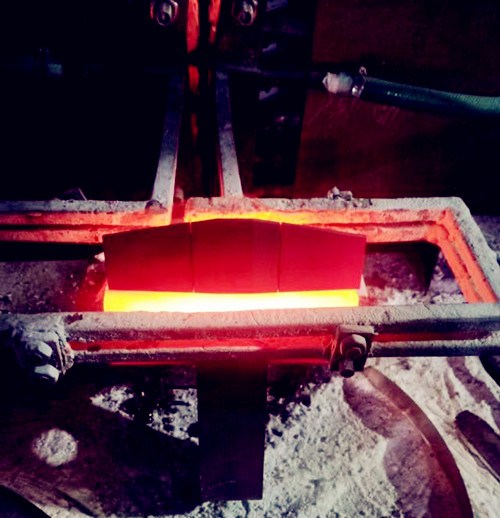
Das Hartlöten von Kohlenstoff-Werkzeugstahl wird am besten vor oder gleichzeitig mit dem Abschreckvorgang durchgeführt. Wird das Hartlöten vor dem Abschrecken durchgeführt, sollte die Solidustemperatur des verwendeten Hartlotes höher sein als der Abschrecktemperaturbereich, damit die Schweißnaht beim Wiedererwärmen auf die Abschrecktemperatur noch eine ausreichende Festigkeit aufweist und nicht versagt. Wenn Hartlöten und Abschrecken zusammen durchgeführt werden, sollte ein Hartlot mit einer Solidustemperatur nahe der Abschrecktemperatur gewählt werden. Legierter Werkzeugstahl hat eine breite Palette von Zusammensetzungen. Das geeignete Hartlot, der Wärmebehandlungsprozess und die Technologie, die das Hartlöten und den Wärmebehandlungsprozess kombiniert, sollten entsprechend der spezifischen Stahlsorte bestimmt werden, um eine gute Verbindungsleistung zu erzielen.
Die Abschrecktemperatur von Schnellarbeitsstahl ist im Allgemeinen höher als die Schmelztemperatur von Silber-Kupfer- und Kupfer-Zink-Loten. Daher muss vor dem Hartlöten abgeschreckt und während oder nach dem Sekundärhärten gelötet werden. Wenn nach dem Hartlöten abgeschreckt werden muss, kann nur das oben erwähnte spezielle Hartlot zum Hartlöten verwendet werden. Beim Hartlöten von Werkzeugen aus Schnellarbeitsstahl ist es sinnvoller, einen Koksofen zu verwenden. Wenn das Hartlot schmilzt, ist das Werkzeug herauszunehmen und sofort unter Druck zu setzen, um das überschüssige Hartlot herauszudrücken, dann in Öl abzuschrecken und anschließend bei 550-570 °C anzulassen.
Beim Hartlöten von Hartmetallklingen und Stahlwerkzeughaltern ist es ratsam, den Lötspalt zu vergrößern und Kunststoffausgleichsdichtungen im Lötspalt anzubringen sowie die Abkühlung nach dem Schweißen zu verlangsamen, um die Lötbelastung zu verringern, Risse zu vermeiden und die Lebensdauer der Hartmetallwerkzeugkomponenten zu verlängern. Nach dem Löten sollten die Flussmittelrückstände auf dem Schweißstück mit heißem Wasser oder einer allgemeinen Schlackenentfernungsmischung abgewaschen und dann mit einer geeigneten Beizlösung gebeizt werden, um die Oxidschicht auf dem Grundwerkzeugstab zu entfernen. Achten Sie jedoch darauf, keine Salpetersäurelösung zu verwenden, um eine Korrosion des Lötmetalls zu vermeiden.