4 Hauptunterschiede zwischen Wolframcarbid und HSS-Schnellarbeitsstahl
Wolframcarbid vs. HSS: Wolframcarbid (oft als "Hartmetallstahl" bezeichnet) und Schnellarbeitsstahl (HSS) werden in industriellen Anwendungen häufig verglichen, weisen jedoch grundlegende Unterschiede in Bezug auf Zusammensetzung, Leistung und Anwendungsszenarien auf. Die Materialauswahl wirkt sich direkt auf die Produktlebensdauer und die Produktionskosten aus, und das Verständnis dieser Unterschiede ermöglicht es Ingenieuren, fundierte Entscheidungen für kritische Komponenten wie Schneidwerkzeuge und Formen zu treffen.
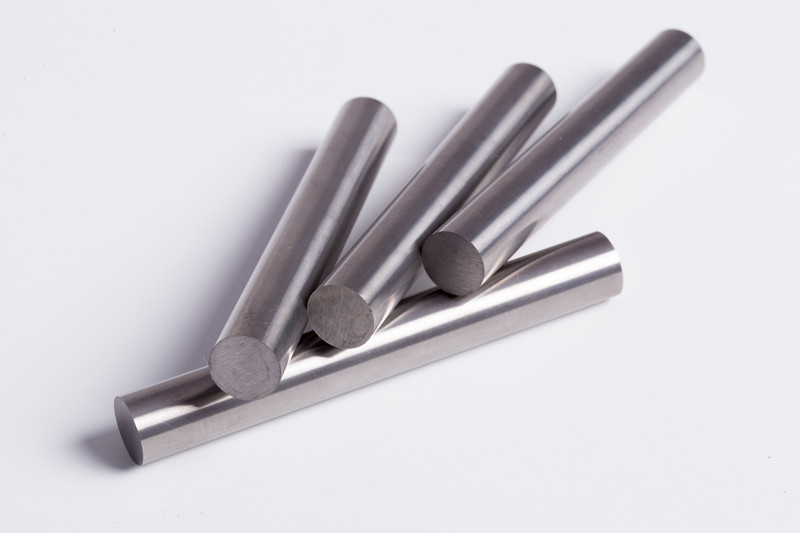
1. Inhärente kompositorische Unterschiede diktieren die Leistung
Wolframcarbid ist ein Hartmetall bestehend aus über 90% Wolframpulver, das durch Hochtemperatursintern mit einer Kobaltmatrix verbunden wird. Diese Struktur ähnelt der Bewehrung von Stahlstäben in Beton, wobei das Kobaltbindemittel (in der Regel 6-12% nach Gewicht) als "Zement" wirkt. Eine Variation des Kobaltgehalts um 1% verändert die Querbruchfestigkeit um ca. 200 MPa und ermöglicht ein präzises Gleichgewicht von Härte und Zähigkeit.
Im Gegensatz dazu ist Schnellarbeitsstahl eine Stahllegierung mit hohem Kohlenstoffgehalt, die 5-20% Wolfram enthält und durch Schmelzen zu einer homogenen Struktur geformt wird. Seine Eigenschaften beruhen auf den festigkeitssteigernden Effekten von Legierungselementen wie Chrom, Vanadium und Molybdän in Mischkristallen. Diese Unterschiede in der Zusammensetzung führen zu einem unterschiedlichen Gefüge: Wolframkarbid weist dicht gepackte polyedrische WC-Körner auf, während HSS eine martensitische Matrix mit dispergierten Karbiden aufweist.
2. Härte und Hitzebeständigkeit: Polarisierte Leistung
Wolfram Karbid erreicht bei Raumtemperatur eine Härte von HRA 89-94 (entspricht HRC 70+) und behält seine Schärfe auch bei der Bearbeitung von Titanlegierungen. Bei 800°C nimmt seine Härte nur um ~10% ab, was auf die außergewöhnliche thermische Stabilität von WC zurückzuführen ist.
Schnellarbeitsstahl mit einem Härtebereich von HRC 63-67 wird bei 600 °C trotz Oberflächenbeschichtungen (z. B. TiN oder AlCrN) deutlich weicher. Eine Fallstudie zur Bearbeitung von Getrieberädern in der Automobilindustrie ergab, dass Hartmetallwerkzeuge die Produktivität im Vergleich zu HSS verdreifachen, wenn auch mit 5× höheren Anschaffungskosten.
3. Herstellungskosten: Divergierende Wirtschaftskurven
Die pulvermetallurgische Herstellung von Wolframcarbid erfordert Sintertemperaturen von mehr als 1.400 °C und einen Energieverbrauch von ~3.500 kWh pro Tonne. Die Volatilität des Kobaltpreises wirkt sich zusätzlich auf die Materialkosten aus. Hartmetalleinsätze werden in der Regel gelötet oder mechanisch geklemmt und bieten einen hohen Wiederverwertungswert.
HSS, das im Lichtbogenofen bei einem Energieverbrauch von ca. 600 kWh pro Tonne geschmolzen wird, kann durch Schmieden oder Walzen plastisch verformt werden. Ein Werkzeughersteller berichtete, dass HSS-Bohrer 15 Mal nachgeschliffen werden können, während Hartmetallwerkzeuge oft nur einmal verwendet werden. Dies schafft komplementäre Kostenprofile: HSS bietet mehr Flexibilität bei der Wartung, während bei Hartmetall die Langlebigkeit im Vordergrund steht.
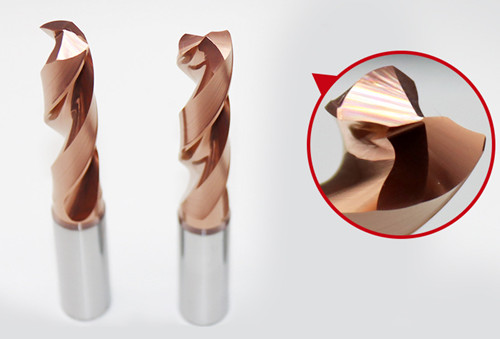
4. Anwendungsszenarien: Abwägung von Wirtschaftlichkeit und Leistung
Wolframcarbid dominiert die CNC-Bearbeitungszentren und erreicht bei Gusseisen Schnittgeschwindigkeiten von 250 m/min - fünfmal schneller als HSS. Bei der intermittierenden Zerspanung (z. B. bei der Bearbeitung von Wellen mit Keilnuten) ist die Schlagfestigkeit von HSS jedoch besser. Eine vergleichende Studie im Flugzeugbau ergab, dass HSS-Werkzeuge bei der Bearbeitung dünnwandiger Aluminiumteile die Rattererscheinungen um 40% reduzieren und die Oberflächengüte verbessern.
Diese Leistungsdichotomie ergibt sich aus den intrinsischen Materialeigenschaften: HSS ist Elastizitätsmodul (~250 GPa) sorgt für Schwingungsdämpfung, während die Steifigkeit von Karbid (~600 GPa) die Schwingungsdämpfung für Stabilität opfert.
Strategische Auswahl: Ein multidimensionaler Ansatz
Ingenieure müssen die Lebenszykluskosten und nicht die Vorlaufkosten bewerten. Ein Formenhersteller, der auf Hartmetallstempel umstellte, verzeichnete 80% höhere Stückkosten, aber eine 6-fach längere Werkzeuglebensdauer, was zu einer Reduzierung der Gesamtkosten um 35% führte. Bei der Produktion von Kleinserien erweist sich die Nachschleifbarkeit von HSS oft als wirtschaftlicher.
Künftige Fortschritte, wie der 3D-Druck komplexer Hartmetallgeometrien, könnten die traditionellen Kostenparadigmen durchbrechen und den Wettbewerb in der Zerspanungsindustrie neu gestalten. Durch die Integration von Materialwissenschaft und Betriebswirtschaft können Ingenieure Leistung und Rentabilität in verschiedenen industriellen Anwendungen optimieren.