How to cut tungsten carbide rod
How to cut tungsten carbide rods? This article will introduce the properties and hardness of the rods to select the correct cutting methods and clamping tools, ensuring that the tungsten carbide rods can be cut correctly and safely. Here are the top ten tungsten carbide rod manufacturers in China. If you need any assistance, please contact us.
1. Hardness Characteristics of Tungsten Carbide Rod
Tungsten carbide (carbide alloy) is a super-hard material sintered from tungsten carbide (WC) and metal binders like cobalt (Co), achieving ultra-high hardness of HRA 88-94 (equivalent to Vickers hardness HV 1400-1850). Its wear resistance exceeds that of high-speed steel by over 10 times . While renowned for extreme wear resistance and compressive strength, it is brittle, requiring avoidance of severe vibration or stress concentration during cutting to prevent cracking.
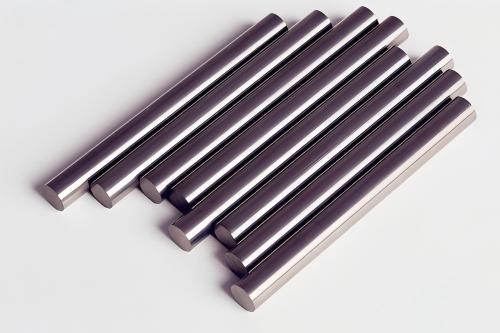
2. Core Cutting Methods for Tungsten Carbide rod
Based on precision, efficiency, and cost needs, methods include:
1. Mechanical Cutting
Diamond Saw Blade Cutting
Suitable for: Straight cutting of rods ≤50mm in diameter with high precision (e.g., tool manufacturing, component processing).
Operation Tips: Use diamond-tipped saw blades (4-16 inches in diameter) with water cooling to reduce temperature and prevent thermal embrittlement. For rods ≤20mm, maintain a speed of 3000-5000 rpm and feed rate ≤10mm/min.
Green silicon Carbide Grinding Wheel Cutting
Suitable for: Rough machining or initial cutting of large-diameter rods (>50mm) with lower costs.
Operation Tips: Use silicon carbide-bonded wheels with cutting fluid to prevent micro-cracks from thermal stress. Drawback: Lower precision requires post-cutting grinding.
2. Non-Mechanical Cutting
Electrical Discharge Machining (EDM)
Suitable for: Complex contours or precision parts (e.g., irregular-shaped holes curved surfaces), especially for super-hard alloys with HRA90+ hardness. Wire cutting is currently the most widely used method for cutting tungsten cemented carbide rods in the cemented carbide industry.
Principle: Material is eroded via high-frequency pulsed discharges without mechanical contact, avoiding stress damage. Capable of cutting rods ≤100mm with ±0.01mm precision, but slower—ideal for small-batch, high-precision needs.
Laser Cutting
Suitable for: Ultra-fine rods ≤10mm or thin slices, prioritizing efficiency and fine processing (e.g., medical devices, electronics).
Principle: High-energy laser melts material for smooth, burr-free cuts, but high equipment costs and potential heat-affected zones in thick materials.
3. Clamping Strategies for Different Rod Diameters
Clamping stability directly impacts cutting precision and safety—classified by diameter:
1. Small-Diameter Rods (≤10mm)
Clamping Tools: Precision vise + V-groove padding blocks
Operation Tips: Wrap rods in soft copper sheets to avoid surface damage; match V-groove angles (common 60° or 90°) to rod diameter, ensuring axis perpendicularity with a 0.02mm dial indicator for φ5mm rods.
2. Medium-Diameter Rods (10-50mm)
Clamping Tools: Hydraulic fixtures + positioning pins
Operation Tips: Adopt symmetrical clamping to prevent deformation; insert positioning pins into pre-machined center holes of rod ends for accuracy. For φ30mm rods, maintain clamping force at 50-80N to avoid slipping or cracking.
3. Large-Diameter Rods (>50mm)
Clamping Tools: Gantry-style fixing frames + adjustable support blocks
Operation Tips: Use multiple support blocks for even weight distribution, avoiding overhanging end vibration; adjust levelness with a dial indicator (error ≤0.1mm/m). For φ100mm rods, place supports 50mm from the cutting point to reduce cantilever deformation.
4. Safety and Quality Control Notes
Protective Gear: Always wear anti-spatter goggles, dust masks, and non-slip gloves to avoid inhaling tungsten carbide dust (hazardous to health).
Cooling Measures: Use cutting fluid or compressed air for mechanical cutting; ensure deionized water purity in EDM to prevent conductive impurities affecting precision.
Post-Cutting Inspection: Check cuts with a magnifier. If burrs or cracks exist, grind with diamond tools to achieve surface roughness Ra≤1.6μm.
5. Conclusion
Cutting tungsten carbide rod requires balancing hardness and brittleness. Choose tools based on diameter and precision: diamond saw blades or EDM for small-diameter precision cuts, silicon carbide wheels for large-diameter roughing. Clamp by diameter to ensure stability, and strictly follow cooling and safety protocols for efficient, accurate processing.