YG6 tungsten carbide
YG6 tungsten carbide, a member of the tungsten-cobalt (WC-Co) alloy family, is renowned for its balanced combination of high hardness, wear resistance, and toughness. Composed of approximately 94% tungsten carbide (WC) and 6% cobalt (Co), this material is engineered to meet the demands of medium-load industrial applications. The cobalt binder phase enhances ductility, while the tungsten carbide matrix ensures exceptional wear resistance. This article provides a comprehensive overview of YG6’s technical specifications, performance characteristics, and practical applications.
1. Composition and Microstructure
YG6 cemented carbide consists of two primary phases:
Tungsten Carbide (WC): ~94% by weight, forming the hard, wear-resistant matrix.
Cobalt (Co): ~6% by weight, acting as a metallic binder that bonds WC grains.
The microstructure features uniformly distributed submicron WC grains (1–2 μm) embedded within a continuous cobalt network. This configuration ensures optimal stress distribution, minimizing crack propagation under mechanical loads.
2. Key Physical and Mechanical Properties
Property | Value | Test Standard |
Hardness (HRA) | ≥89.5 | ISO 3738 |
Transverse Rupture Strength | ≥1900 MPa | ISO 3327 |
Impact Toughness | 2.6 J/cm² | ASTM E23 |
Density | 14.6–15.00 g/cm³ | GB/T 3850 |
Thermal Conductivity | 80 W/(m·K) | ASTM E1461 |
Thermal Stability | Maintains properties at 800–900°C | DIN 50100 |
Structural Advantages:
High Hardness: WC grains (2200–2400 HV) provide superior abrasion resistance.
Enhanced Toughness: The cobalt binder absorbs impact energy, reducing brittleness.
Thermal Resistance: Stable performance in high-temperature environments up to 900°C.
3. Industrial Applications
YG6 is widely utilized across industries requiring durability and precision:
3.1 Metal Cutting Tools
Components: Inserts for turning, milling, and drilling.
Performance:
40% higher machining efficiency for cast iron compared to high-speed steel (HSS).
Dimensional accuracy within ±5 μm during finishing operations.
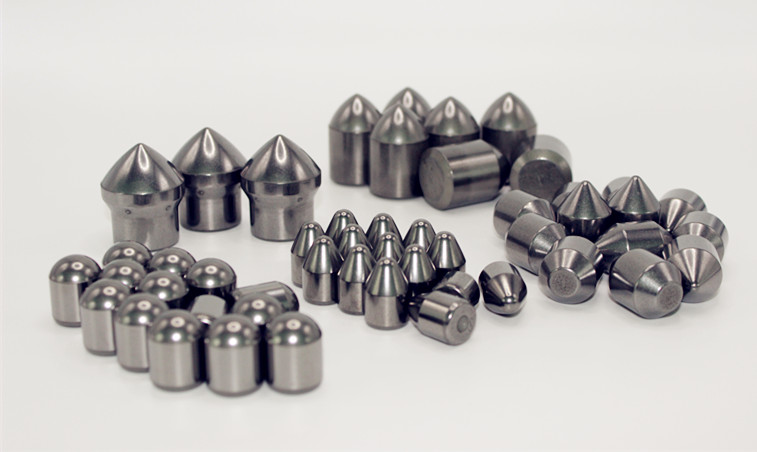
3.2 Stamping and Forming Dies
Applications: Stainless steel sheet forming, automotive panel dies.
Advantages:
5× longer service life than conventional tool steel dies.
Springback control ≤10 μm for high-precision forming.
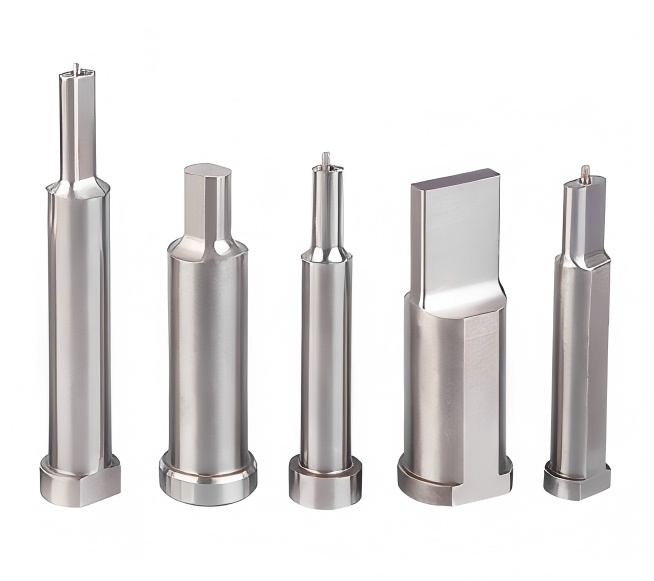
3.3 Mining and Geological Tools
Components: Rock drill bits, tunneling equipment.
Durability:
Operates continuously for 60+ hours in medium-hard rock formations.
8× higher wear resistance than alloy steel counterparts.
3.4 Wear-Resistant Components
Examples: Bearings, gears, conveyor scraper blades.
Performance Metrics:
Wear rate: 0.01 mm per 1000 operating hours.
Contact fatigue strength: 900 MPa.
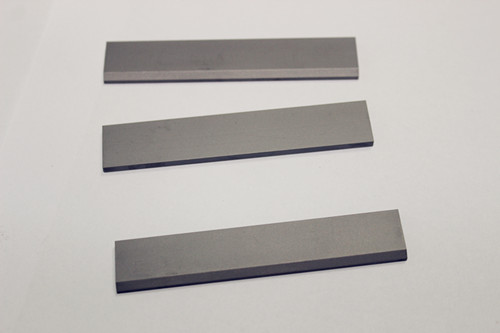
4. Operational Guidelines
4.1 Environmental Limitations
Temperature: Avoid prolonged exposure above 800°C to prevent cobalt oxidation.
Corrosion Resistance: Susceptible to strong acids/alkalis; surface coatings (e.g., CrN, TiAlN) recommended for harsh environments.
4.2 Maintenance Best Practices
Regrinding: Use diamond grinding wheels (120–200 mesh) with a maximum depth of 0.1 mm per pass.
Post-Processing: Sandblast with 80-mesh alumina at 0.2 MPa to eliminate microcracks.
Storage: Maintain humidity below 40% in anti-corrosion packaging.
4.3 Failure Prevention
Stress Management: Finite element analysis (FEA) to limit localized stress to <500 MPa.
Wear Monitoring: Replace cutting tools when flank wear (VBmax) reaches 0.3 mm.
5. Comparative Analysis with Similar Grades
Grade | Co Content (%) | Hardness (HRA) | TRS (MPa) | Recommended Applications |
YG3 | 3 | 91.0 | 1400 | Precision finishing (low vibration) |
YG6 | 6 | 89.5 | 1900 | General machining (medium load) |
YG8 | 8 | 89.0 | 2100 | Heavy-duty cutting/impact operations |
6. Quality Control and Recycling
6.1 Certification Standards
Density Tolerance: ±0.15 g/cm³ to ensure defect-free microstructure.
Metallographic Inspection: ASTM B657 compliance for WC grain uniformity.
6.2 Sustainable Practices
Recycling Efficiency: 95% tungsten and 92% cobalt recovery via zinc melt processes (ISO 14001 certified).
7. Future Development Trends
Nanostructured Variants: WC grain sizes <0.5 μm to enhance strength (target TRS ≥2500 MPa).
Advanced Coatings: Diamond-like carbon (DLC) or multilayer (TiAlN/AlCrO) coatings to reduce friction and extend tool life.
Additive Manufacturing: Laser-based techniques to produce complex geometries with minimal material waste.
Conclusion
YG6 cemented carbide remains a cornerstone material for industries demanding a balance of hardness, toughness, and thermal stability. Its performance in medium-load applications—from precision machining to wear-intensive environments—highlights its versatility. By adhering to operational guidelines and leveraging emerging technologies like nanostructuring and advanced coatings, users can further optimize efficiency and sustainability. As industrial requirements evolve, YG6 continues to adapt, solidifying its role in modern manufacturing.