YG10X carbide products and its uses
Cemented carbide, with its high hardness, high wear resistance and excellent mechanical properties, plays an irreplaceable role in the industrial field. Among them, YG10X carbide, as a typical tungsten-cobalt cemented carbide, is widely used in many industrial fields due to its unique composition and excellent mechanical properties. This article will deeply explore the composition, specific performance, production steps, application fields and share of YG10X, and summarize its development prospects.
1.Composition:
The main components of YG10X are tungsten carbide (WC) and cobalt (Co), and a small amount of titanium (Ti), niobium (Nb) and other elements are added to improve its comprehensive performance. Tungsten carbide, as a hard phase, gives the alloy extremely high hardness and wear resistance; cobalt, as a bonding metal, provides good toughness and bending strength. Specifically, the cobalt content in YG10X is about 10%, and the rest is mainly tungsten carbide. In addition, the selection of ultrafine grains (such as 0.6μm-0.8μm) further improves its wear resistance and strength. The following figure is a metallographic picture of YG10X for reference.
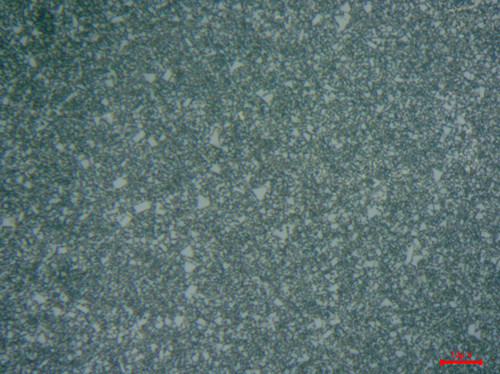
2.Specific performance:
YG10X cemented carbide has a series of excellent properties: High hardness: Its hardness can usually reach above 91.5HRA, which enables it to resist wear under high load.
High strength: The bending strength exceeds 3600N/mm², ensuring the stability of the alloy in complex stress environments.
Good toughness: The addition of cobalt makes YG10X have good impact toughness and is not prone to chipping during cutting.
Excellent corrosion resistance: Under certain conditions, YG10X can resist chemical corrosion and extend its service life.
WC | Co | Grain size (μm) | Hardness(HRA) | Density(g/cm³) | TRS (Mpa) |
90% | 10% | 0.8 | 91.5 | 14.35 | 3600 |
The production process of YG10X cemented carbide includes the following key steps:
Ingredients: Accurately weigh the raw material powder according to the predetermined composition ratio, including tungsten carbide, cobalt, titanium, niobium and other elements. Mixing and crushing: Add the raw material powder to the wet ball mill, add an appropriate amount of alcohol or other media for wet grinding, and fully mix and crush it to the required particle size.
Drying and sieving: The mixed powder is dried and then sieved to remove impurities and agglomerates.
Adding molding agent: Add molding agent such as wax or glue to the dried powder, dry and sieve again to obtain a mixture.
Granulation and pressing: The mixture is granulated and pressed to form the desired blank shape. Sintering: The blank is placed in a vacuum low-pressure sintering furnace for sintering. The temperature is usually close to the melting point of cobalt (about 1300-1500℃), so that the hardened phase and the bonding metal form a eutectic alloy.
Cooling and inspection: After sintering, the finished product is cooled, and then non-destructive ultrasonic flaw detection and other dimensional accuracy inspections are performed on the finished product.
4.Application fields and share:
YG10X cemented carbide is widely used in many industrial fields due to its unique properties: Tool manufacturing: YG10X cemented carbide round bars are suitable for manufacturing high-precision tools such as fine-diameter micro drills, end mills, rotary files, etc., for processing hard materials. Drills and milling cutters produced with YG10X carbide grades can process alloy materials with a hardness of 45-50HRC, such as common steel, alloy steel, non-ferrous metals, iron castings. Drills and milling cutters produced by YG10X are cost-effective and currently dominate the low-end and mid-range markets. The main users include China, India, Southeast Asia, Turkey and some European countries. If you need YG10X round bars, please contact us.
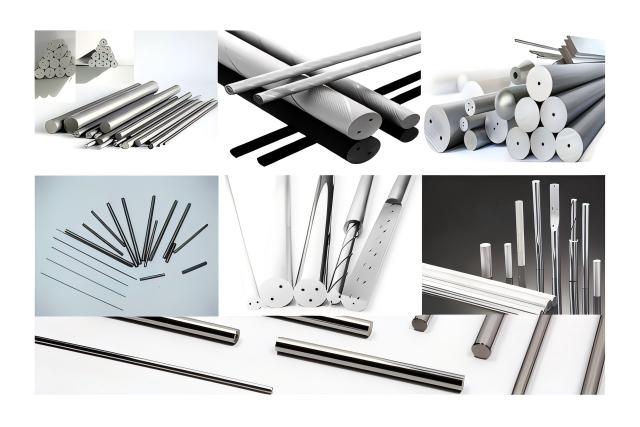
Mold manufacturing: Suitable for making powder pressing molds, drawing molds and carbide molds for forming metal materials.
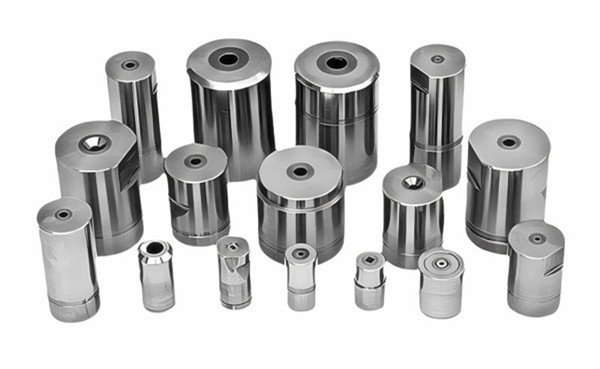
Aerospace: In the aerospace field, YG10X is used to manufacture high-speed cutting tools and engine parts to meet performance requirements under extreme working conditions.
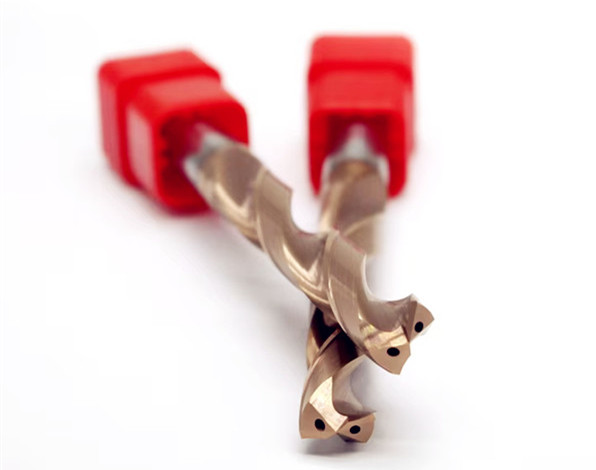
Automotive industry: In the automotive manufacturing industry, YG10X is used to manufacture key components such as engine parts, transmission systems and brake systems.
Oil and gas industry: YG10X can produce carbide sealing rings and sleeves for valves and pump bodies.
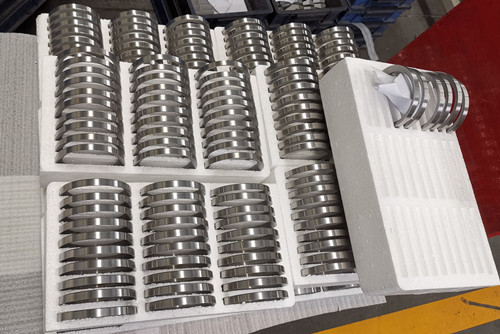
Although it is difficult to accurately count the specific market share data, YG10X cemented carbide is increasingly widely used in the above-mentioned fields, and its market share continues to grow. Especially in the field of high-end manufacturing, YG10X has won the favor of customers with its excellent performance. At present, the round bar share of YG10X accounts for the highest proportion of YG10X products and the largest usage, mainly used to produce industrial tools.
5.Development prospects with the continuous upgrading and transformation of the manufacturing industry, the performance requirements for cemented carbide are also getting higher and higher. YG10X cemented carbide has broad development prospects in the field of high-end manufacturing due to its unique composition and excellent performance. In the future, with the continuous advancement of technology and further reduction of costs, the application field of YG10X cemented carbide will be further expanded, and the market share will continue to grow.
6.Summary YG10X cemented carbide is widely used in many fields such as tool manufacturing, mold manufacturing, aerospace and automotive industries due to its high hardness, high strength, good toughness and excellent corrosion resistance. Its unique composition and excellent performance make it a preferred material in the field of high-end manufacturing. In the future, with the continuous advancement of technology and the continuous expansion of the market, the application prospects of YG10X cemented carbide will be broader.