What is hardmetal and its uses
What is hardmetal, another name for hardmetal is cemented carbide. As an important engineering material, Hardmetal has been widely used in mechanical processing, mining, aerospace and other fields due to its excellent hardness, wear resistance and high temperature stability. This paper will discuss the composition, preparation process, microstructure, mechanical properties and application of Hardmetal in detail, aiming to provide reference for researchers and engineering technicians in related fields.
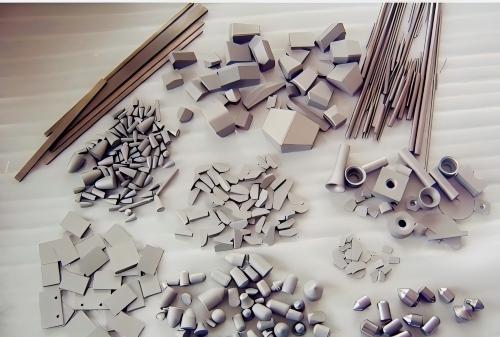
1.Introduction Hardmetal is a composite material made of refractory metal carbides (such as tungsten carbide WC, titanium carbide TiC, etc.) and bonding metals (such as cobalt Co, nickel Ni, etc.) through powder metallurgy. Since its advent in the 1920s, Hardmetal has quickly become a research hotspot in the field of materials science and engineering due to its excellent mechanical properties and wide application prospects.
2. Composition and classification of Hardmetal
2.1 Composition Hardmetal is mainly composed of two parts: Hard phase: usually refractory metal carbides such as wolfram carbide (WC), titanium carbide (TiC), tantalum carbide (TaC), etc. These carbides have extremely high hardness and wear resistance and are the main load-bearing phase of Hardmetal. Binder phase: usually metals such as cobalt (Co) and nickel (Ni). The function of the binder phase is to bind the hard phase particles together and provide certain toughness and impact resistance.
2.2 Classification According to the difference between the hard phase and the binder phase, Hardmetal can be divided into the following categories: WC-Co Hardmetal: This is the most common type of Hardmetal, widely used in cutting tools, molds and wear-resistant parts. WC-TiC-Co Hardmetal: By adding TiC, the high temperature performance and oxidation resistance of the alloy are improved, which is suitable for high-speed cutting. TiC-Ni-Mo Hardmetal: With TiC as the hard phase and Ni-Mo as the binder phase, it has high hardness and wear resistance and is suitable for high-precision processing.
3. Preparation process of Hardmetal
3.1 Powder preparation The preparation of Hardmetal first requires obtaining high-purity hard phase and binder phase powders. Common methods include: Carbonization method: by reacting metal powder with carbon powder at high temperature to generate carbide. Reduction method: by reducing metal oxides to obtain metal powder.
3.2 Mixing and molding Mix the hard phase and binder phase powders in a certain proportion and make them evenly distributed through processes such as ball milling. The mixed powder is pressed and molded to form a blank of the desired shape.
3.3 Sintering The formed blank is sintered at high temperature to melt the binder phase and wet the hard phase particles to form a dense alloy structure. The sintering process has a decisive influence on the final performance of Hardmetal.
4. Microstructure of Hardmetal
4.1 Distribution of hard phase and binder phase The microstructure of Hardmetal is mainly composed of hard phase particles and binder phase matrix. The size, shape and distribution of hard phase particles have an important influence on the performance of the alloy. Fine hard phase particles can improve the hardness and wear resistance of the alloy, while uniform distribution helps to improve the toughness of the alloy.
4.2 Grain boundaries and phase boundaries Grain boundaries and phase boundaries in Hardmetal are important factors affecting its mechanical properties. The strength of the grain boundary and the bonding state of the phase boundary directly determine the fracture resistance and wear resistance of the alloy.
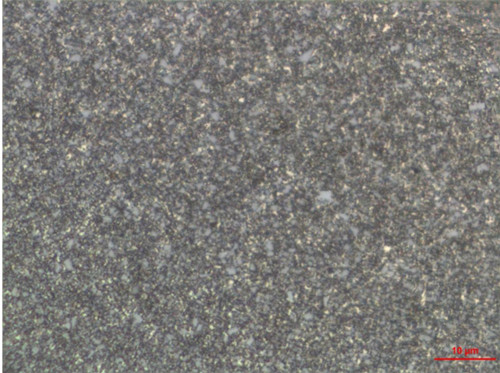
5.Mechanical properties of Hardmetal
5.1 Hardness The hardness of Hardmetal mainly depends on the type and content of the hard phase. The hardness of WC-Co Hardmetal is usually between HRA 88-94, which is much higher than that of ordinary steel.
5.2 Wear resistance The wear resistance of Hardmetal is one of its most important properties. Due to the high hardness of the hard phase and the good toughness of the bonding phase, Hardmetal exhibits excellent wear resistance under high-speed cutting and heavy load conditions. 5.3 Bending strength The bending strength of Hardmetal is mainly affected by the bonding phase content and the particle size of the hard phase. Appropriate bonding phase content can improve the bending strength of the alloy, but too high bonding phase content will reduce the hardness of the alloy.
5.4 High temperature performance Hardmetal can still maintain high hardness and strength at high temperatures, which makes it widely used in high temperature cutting and hot processing.
6.Application of Hardmetal
6.1 Cutting tools Hardmetal is widely used in cutting tools such as turning tools, milling cutters, and carbide drill bits. For example, Hardmetal rods are used to process milling cutters and drill bits. Its high hardness and wear resistance make it perform well under high-speed cutting and heavy-load cutting conditions.
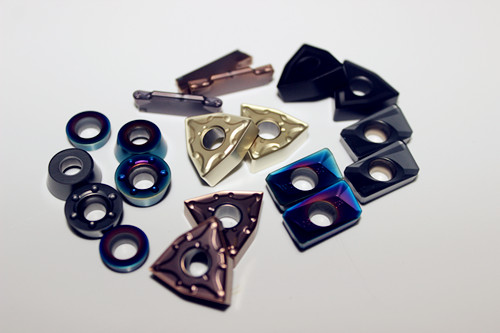
6.2 Mining tools Hardmetal is used to manufacture mining tools such as rock drill bits and picks. Its high wear resistance and impact resistance make it perform well in harsh mining environments.
6.3 Dies Hardmetal is used to manufacture cold heading dies, wire drawing dies and other dies. Its high hardness and wear resistance make it have a long life under high pressure and high wear conditions.
6.4 Aerospace Hardmetal is used to manufacture high-temperature components and wear-resistant parts in the aerospace field. Its excellent high temperature performance and wear resistance make it perform well in extreme environments.
7.Research and development trends of Hardmetal
7.1 Nano Hardmetal With the development of nanotechnology, nano Hardmetal has become a research hotspot. Nano Hardmetal has higher hardness and toughness, and is expected to be used in ultra-precision machining and micro-nano manufacturing.
7.2 Coating technology By depositing wear-resistant coatings (such as TiN, TiAlN, etc.) on the surface of Hardmetal, its wear resistance and service life can be further improved. Coating technology has become an important direction for Hardmetal research.
7.3 New binder phase Studying new binder phases (such as Fe, Ni-based alloys) to improve the toughness and high-temperature performance of Hardmetal is an important direction for future development.
8. Conclusion As an important engineering material, Hardmetal has an important position in the field of materials science and engineering due to its excellent mechanical properties and broad application prospects. With the research progress of nanotechnology, coating technology and new binder phases, the performance of Hardmetal will be further improved and its application field will continue to expand.