Прочность карбида вольфрама на сжатие и предел текучести при растяжении
Карбид вольфрама образует плотную спеченную кристаллическую структуру за счет высокотемпературного соединения атомов вольфрама и углерода, наделяя материал исключительной твердостью. Как керамический материал, чистый карбид вольфрама обладает высокой твердостью и хрупкостью, при относительно низкой прочности на разрыв, на которую существенно влияют производственные процессы (например, плотность спекания, размер зерна). Чистый карбид вольфрама имеет предел прочности на разрыв 344 МПа. Карбид вольфрама промышленного качества обычно сочетается со связующими металлами, такими как кобальт (Co) и никель (Ni), чтобы скрепить частицы карбида вольфрама, существенно улучшая хрупкость и повышая прочность на разрыв. Этот композитный материал обычно называют цементированным карбидом. Прочность на сжатие цементированных карбидов вольфрама обычно составляет от 4 000 до 6 000 МПа (580 151-870 226 psi).что эквивалентно выдерживанию 400-600 килограммов на квадратный миллиметр. В таблице ниже представлены пределы прочности и текучести цементированного карбида вольфрама для конкретных марок:
Цементированный карбид | Класс | Химический состав | Прочность на разрыв(MPa) | Предел текучести(MPa) |
WC-Co Низкий уровень кобальта | YG6 | WC-6%Co | 1400~1800 | 1500~1800 |
WC-Co Средний кобальт | YG8 | WC-8%Co | 1800~2200 | 1600~2000 |
WC-Co Высокое содержание кобальта | YG15 | WC-15%Co | 2400~2800 | 1200~1500 |
Ультрамелкий размер зерна WC-Co | YG10X | Ультрамелкий размер зерна WC-10% Co | 3000~3500 | 2000~2500 |
WC-TiC-Co | YT15 | WC-15%TiC-6%Co | 1100~1500 | 1000~1300 |
WC-Ni-Fe | YN10 | WC-10%Ni-5%Fe | 1600~2000 | 1400~1700 |
Предел текучести при растяжении цементированного карбида вольфрама отражает способность материала сопротивляться разрушению при растяжении. Во время испытания концы образца зажимаются в машине для испытания на растяжение. При увеличении усилия растяжения точка перехода материала от упругой деформации к пластической является пределом текучести при растяжении. Из-за значительной хрупкости цементированных карбидов предел текучести при растяжении карбида вольфрама заметно ниже предела прочности при сжатии, обычно составляя от 1000 до 1500 МПа. Эта особенность требует особого внимания к предотвращению концентрации растягивающих напряжений при проектировании деталей из карбида вольфрама, например, при использовании закругленных переходов на кромках режущего инструмента.
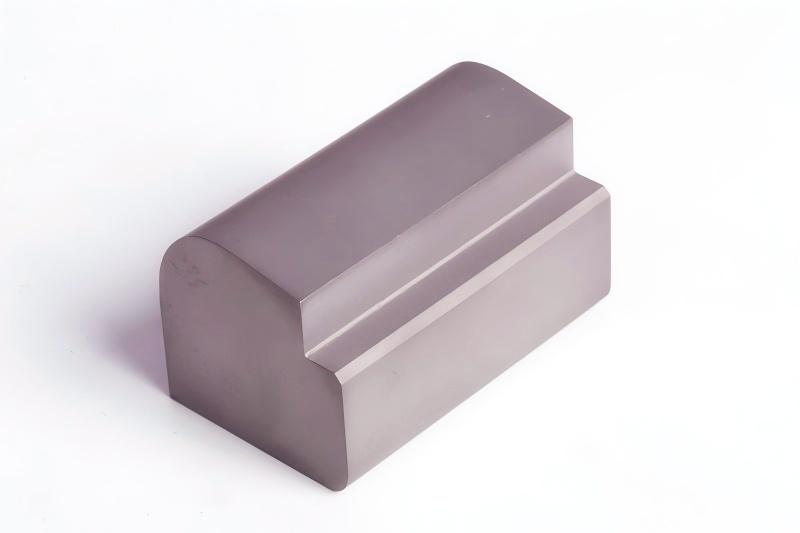
Соотношение состава материала напрямую влияет на механические свойства. При увеличении содержания кобальта в качестве связующей фазы на 1% прочность на сжатие снижается примерно на 80 МПа, но вязкость повышается. Например, конкретная модель сплава для бурения горных пород с содержанием кобальта 6% достигает прочности на сжатие 5800 МПа, в то время как у режущей пластины с содержанием кобальта 15% прочность на сжатие снижается до 4200 МПа. Контроль размера зерна карбида вольфрама в диапазоне от 0,5 до 2 микрометров позволяет достичь оптимального баланса прочности; слишком мелкое зерно может привести к неравномерному распределению связующей фазы, а слишком крупное зерно может привести к образованию трещин.
Изменение температуры нелинейно влияет на показатели прочности. Экспериментальные данные показывают, что при превышении рабочей температуры 600°C прочность карбида вольфрама на сжатие снижается со скоростью 0,8% на градус Цельсия. Например, прочность на сжатие уплотнительного кольца авиадвигателя, работающего при температуре 800°C, снижается с 5200 МПа при комнатной температуре до 3200 МПа. Основной причиной снижения прочности при высоких температурах является распространение микротрещин под действием термического напряжения; добавление таких элементов, как хром и ванадий, может повысить высокотемпературную стабильность.
При бурении нефтяных скважин резцы PDC должны одновременно выдерживать сжатие пласта и ударное растяжение. В конкретной модели резцов используется градиентная структура: в поверхностном слое - зерна карбида вольфрама, рафинированные до 0,8 микрометра, а в сердцевине - 2-микрометровые зерна. Испытания показали прочность на сжатие 5500 МПа и растяжение 1300 МПа, что позволило увеличить срок службы 40% по сравнению с однородной структурой. При резке металла угол наклона режущего инструмента напрямую влияет на напряженное состояние; при отрицательном угле наклона силы резания преобразуются в сжимающее напряжение, что позволяет полностью использовать преимущество материала в прочности на сжатие.
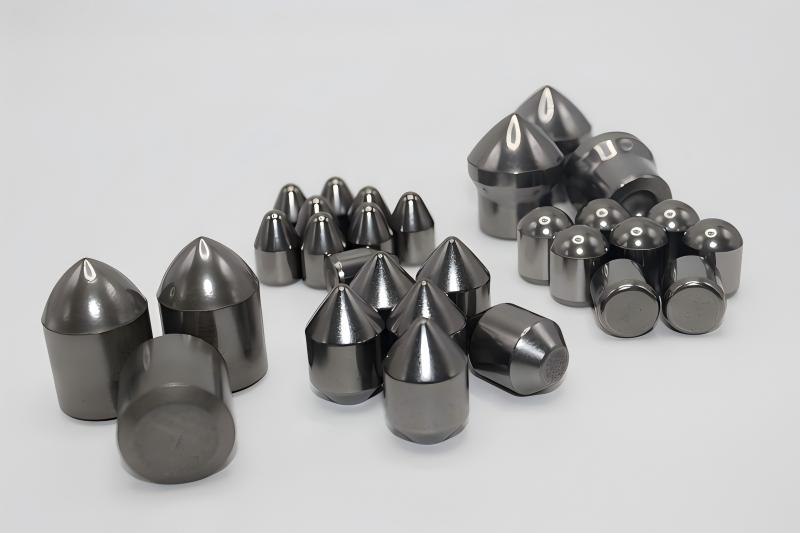
Контроль качества требует особого внимания к обнаружению дефектов. Пористость, превышающая 0,05%, может снизить прочность на сжатие на 15%. Ультразвуковой контроль позволяет обнаружить внутренние дефекты размером более 0,1 мм. Анализ отказов партии штампов для холодной штамповки выявил внутри штампа не спеченные поры размером 0,3 мм, из-за чего фактическая прочность на сжатие составила всего 72% от номинального значения.
Исследования в области модификации материалов достигли прорыва: нано-Слоистый структурированный карбид вольфрама сохраняет прочность на сжатие 4800 МПа при увеличении прочности на растяжение до 1800 МПа. Эта структура, созданная путем поочередного нанесения слоев карбида вольфрама толщиной 5 нм и слоев металла толщиной 2 нм, эффективно препятствует распространению трещин. Лабораторные данные показывают, что вязкость разрушения модифицированного материала увеличилась в 2,3 раза, и он нашел применение в производстве прецизионных штамповочных матриц.
При выборе необходимо всесторонне учитывать условия работы. Для применения в условиях частых ударных нагрузок следует выбирать составы с меньшей прочностью на сжатие, но большей вязкостью. В условиях длительного воздействия высокого давления приоритет отдается материалам с максимальной прочностью на сжатие. Например, после замены головки молотка шахтной дробилки на высококобальтовую формулу (12%), хотя прочность на сжатие снизилась до 4500 МПа, срок службы увеличился в 3 раза, поскольку повышенная вязкость материала эффективно противостояла циклическим ударам.
Анализ случаев разрушения показывает взаимозависимость показателей прочности. Разрушение сепаратора прецизионного подшипника было связано с тем, что предел прочности на растяжение исходного материала составлял всего 980 МПа, что ниже проектного требования в 1200 МПа. Дальнейший анализ показал, что низкая температура спекания привела к недостаточной прочности сцепления границ зерен; хотя твердость соответствовала стандарту, фактическая прочность была недостаточной. Этот случай демонстрирует, что при выборе материала нельзя полагаться только на твердость; необходимо проводить комплексные испытания механических свойств.
Наша компания входит в десятку крупнейших в Китае производители цементированного карбида. Если вам нужны изделия из цементированного карбида, пожалуйста связаться с нами.