Parâmetros da liga de carboneto de tungsténio à base de níquel
1. A composição química determina as propriedades fundamentais. Nas ligas de WC à base de níquel, o níquel actua como o elemento base, constituindo normalmente 60% - 85% da composição. Em alguns componentes de ligas aeroespaciais personalizadas, o teor de níquel atinge 75%, conferindo uma excelente tenacidade e resistência à corrosão. Carboneto de tungsténio (WC) é a principal fase de reforço, geralmente presente em 15% - 40%. Para placas de desgaste em peças de ligas de maquinaria mineira, um teor de WC de 30% aumenta significativamente a dureza da superfície. Para além do níquel e do WC, são frequentemente adicionados elementos como o crómio (Cr), o molibdénio (Mo) e o nióbio (Nb). O crómio aumenta a resistência à oxidação; por exemplo, as ferramentas de corte de liga que operam em ambientes de alta temperatura contêm 5% - 15% Cr, prevenindo eficazmente a oxidação da superfície. O molibdénio aumenta a resistência a altas temperaturas; nos componentes de motores aeronáuticos, a sua adição permite que a liga mantenha uma boa resistência mesmo a 800°C.
2.Variação significativa dos indicadores de dureza. A dureza das ligas de WC à base de níquel varia consideravelmente em função das técnicas de processamento e das aplicações. As ligas preparadas por metalurgia do pó e sinterizadas podem atingir níveis de dureza de HRC 60 - 70. Nas fábricas de peças automóveis, os moldes produzidos desta forma suportam dezenas de milhares de ciclos de estampagem de metal sem desgaste significativo. A soldadura por sobreposição (revestimento duro) produz normalmente camadas de liga com dureza de cerca de HV 800 - 1200. A aplicação de uma liga de WC à base de níquel através de soldadura por sobreposição nos rebordos dos lábios das garras das gruas portuárias melhora significativamente a resistência ao desgaste. As garras que anteriormente necessitavam de ser substituídas de seis em seis meses podem durar até dois anos após a aplicação de revestimento duro.
3. Valores de densidade relativamente estáveis. A densidade das ligas de WC à base de níquel varia normalmente entre 10 e 12 g/cm³. Esta densidade é crucial quando se fundem peças de ligas. Por exemplo, uma fundição que produzia grandes assentos de rolamentos em liga sofreu desvios de peso significativos nas peças fundidas devido às flutuações da composição da liga que afectavam a densidade. Normalmente, um maior teor de níquel e um menor teor de WC resultam numa menor densidade, enquanto um maior teor de WC aumenta a densidade. O controlo rigoroso da densidade é essencial para os componentes em liga de instrumentos de precisão, para garantir que o peso cumpre as especificações do projeto.
4. excelente desempenho a altas temperaturas. As ligas WC à base de níquel apresentam um desempenho excecional em ambientes de alta temperatura. A sua gama de temperaturas de funcionamento típica é de 600°C - 1000°C. Em reparações de soldaduras de tubos de caldeiras para centrais térmicas, a utilização de varetas de soldadura de ligas de WC à base de níquel permite que os tubos mantenham uma boa resistência ao desgaste e força sob a ação do vapor de alta temperatura a 850°C. A 900°C, a resistência à tração da liga pode ainda exceder os 500 MPa. Por exemplo, a superfície da mesa de rolos do forno de reaquecimento de uma siderurgia, revestida com liga de WC à base de níquel, apresentou um desgaste mínimo sob a pressão de laminagem de biletes de aço a 950°C, reduzindo drasticamente a frequência de substituição dos rolos.
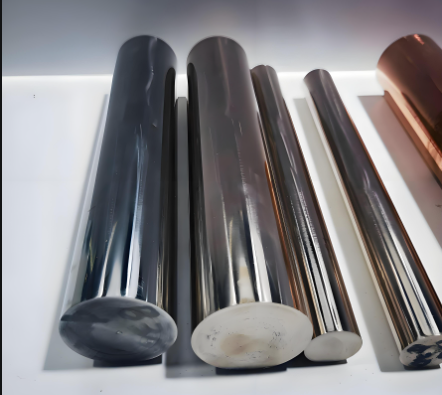
5. resistência excecional ao desgaste. A resistência ao desgaste da liga está intimamente relacionada ao seu teor de WC. Usando a liga de WC à base de níquel para revestimentos de moinhos de bolas em minas, onde o atrito durante a moagem de minério é intenso, os revestimentos com teor de WC 35% duram 5 vezes mais do que os revestimentos de aço padrão. Nas linhas de produção de cimento, a utilização de placas de desgaste de liga de WC à base de níquel nos cotovelos dos tubos que transportam cimento apresenta um desgaste mínimo após mais de um ano, enquanto as placas normais se desgastam em meses. Os tratamentos de superfície, como a refusão a laser, podem aumentar ainda mais a resistência ao desgaste; uma fábrica de máquinas aumentou a vida útil dos moldes de liga 30% após a refusão a laser da superfície.
6. resistência à corrosão varia. As ligas de WC à base de níquel apresentam uma resistência à corrosão diferente consoante o meio corrosivo. Em soluções diluídas de ácido sulfúrico, as ligas com maior teor de Mo demonstram melhor resistência à corrosão. Algumas fábricas de produtos químicos utilizam estas ligas para lâminas de agitadores de vasos de reação, apresentando apenas uma ligeira corrosão superficial após dois anos em ácido sulfúrico diluído. Em ambientes de água do mar, as ligas com Cr e Mo resistem eficazmente à corrosão por iões cloreto. Os componentes fabricados a partir de ligas WC à base de níquel em equipamento de plataformas petrolíferas offshore mantêm um bom desempenho apesar da imersão prolongada em água do mar e da lavagem, evitando falhas induzidas pela corrosão.
7.Expansão térmica O coeficiente tem impacto na aplicação. O coeficiente de expansão térmica (TEC) das ligas de WC à base de níquel é tipicamente (8 - 12) × 10-⁶/°C. Este parâmetro é vital para a montagem de equipamento a alta temperatura. Por exemplo, na montagem de pás de turbinas de motores aéreos no cubo do disco, o TEC dos materiais tem de corresponder. Uma diferença significativa pode gerar tensões térmicas elevadas durante os ciclos de temperatura de arranque/desligamento do motor, causando potencialmente o afrouxamento ou a fratura da lâmina. A conceção de juntas de dilatação para tubos de alta temperatura também exige que se tenha em conta o CET da liga para garantir o livre movimento térmico e evitar danos por tensão.
8. A soldadura apresenta desafios. A soldadura de ligas de WC à base de níquel requer processos especializados. Devido à elevada dureza e ponto de fusão do WC, a soldadura é propensa a fissuras e porosidade. A utilização de métodos de soldadura incorrectos durante a reparação de componentes pode resultar em soldaduras muito fissuradas, levando à rejeição da peça. Uma soldadura adequada necessita de eléctrodos especializados e de uma corrente e velocidade de soldadura controladas. O pré-aquecimento dos componentes a 200°C - 300°C antes da soldadura e a implementação de um arrefecimento lento após a soldadura são essenciais para evitar a fissuração por tensão térmica.
A nossa empresa está entre as dez maiores empresas da China fabricantes de carboneto de tungsténio. Se necessitar de produtos de metal duro, por favor contactar-nos.