Parameter einer Wolframkarbidlegierung auf Nickelbasis
1. die chemische Zusammensetzung bestimmt die grundlegenden Eigenschaften. In WC-Legierungen auf Nickelbasis fungiert Nickel als Basiselement und macht in der Regel 60% - 85% der Zusammensetzung aus. In einigen kundenspezifischen Bauteilen aus Luft- und Raumfahrtlegierungen erreicht der Nickelgehalt 75% und verleiht ihnen eine hervorragende Zähigkeit und Korrosionsbeständigkeit. Wolframcarbid (WC) ist die wichtigste Verstärkungsphase und liegt im Allgemeinen bei 15% - 40%. Bei Verschleißplatten in Bergbaumaschinenlegierungen erhöht ein WC-Gehalt von 30% die Oberflächenhärte erheblich. Neben Nickel und WC werden häufig Elemente wie Chrom (Cr), Molybdän (Mo) und Niob (Nb) hinzugefügt. Chrom erhöht die Oxidationsbeständigkeit; zum Beispiel enthalten legierte Schneidwerkzeuge, die in Hochtemperaturumgebungen eingesetzt werden, 5% - 15% Cr, wodurch die Oxidation der Oberfläche wirksam verhindert wird. Molybdän erhöht die Hochtemperaturfestigkeit; bei Komponenten für Flugzeugtriebwerke ermöglicht sein Zusatz der Legierung, selbst bei 800°C eine gute Festigkeit zu behalten.
2. signifikante Schwankungen bei den Härteindikatoren. Die Härte von WC-Legierungen auf Nickelbasis variiert je nach Verarbeitungsverfahren und Anwendung erheblich. Pulvermetallurgisch hergestellte und gesinterte Legierungen können Härtegrade von HRC 60 - 70 erreichen. In Automobilfabriken überstehen die auf diese Weise hergestellten Formen Zehntausende von Prägezyklen ohne nennenswerten Verschleiß. Beim Auftragschweißen (Hardfacing) werden in der Regel Legierungsschichten mit einer Härte von etwa HV 800 - 1200 erzeugt. Das Auftragen einer WC-Legierung auf Nickelbasis durch Auftragsschweißen auf die Lippenkanten von Hafenkrangreifern verbessert die Verschleißfestigkeit erheblich. Greifer, die früher alle sechs Monate ausgetauscht werden mussten, können nach dem Auftragen der Panzerung bis zu zwei Jahre halten.
3. relativ stabile Dichtewerte. Die Dichte von WC-Legierungen auf Nickelbasis liegt normalerweise zwischen 10 und 12 g/cm³. Diese Dichte ist beim Gießen von Legierungsteilen von entscheidender Bedeutung. Eine Gießerei, die große Lagersitze aus einer Legierung herstellt, musste beispielsweise feststellen, dass das Gewicht der Gussteile aufgrund von Schwankungen in der Legierungszusammensetzung, die sich auf die Dichte auswirken, erheblich abweicht. Normalerweise führen ein höherer Nickelgehalt und ein geringerer WC-Gehalt zu einer geringeren Dichte, während ein höherer WC-Gehalt die Dichte erhöht. Eine strenge Kontrolle der Dichte ist für Komponenten aus Präzisionsinstrumentenlegierungen unerlässlich, um sicherzustellen, dass das Gewicht den Konstruktionsspezifikationen entspricht.
4. herausragende Hochtemperaturleistung. WC-Legierungen auf Nickelbasis weisen eine außergewöhnliche Leistung in Hochtemperaturumgebungen auf. Ihr typischer Betriebstemperaturbereich liegt zwischen 600°C und 1000°C. Bei der Reparatur von Schweißnähten von Kesselrohren in Wärmekraftwerken ermöglicht die Verwendung von Schweißdrähten aus einer WC-Legierung auf Nickelbasis die Beibehaltung einer guten Verschleißfestigkeit und Festigkeit der Rohre unter der scheuernden Wirkung von 850°C heißem Dampf. Bei 900 °C kann die Zugfestigkeit der Legierung immer noch 500 MPa übersteigen. Die Oberfläche des mit einer WC-Legierung auf Nickelbasis beschichteten Rollgangs eines Stahlwerks zeigte beispielsweise nur minimalen Verschleiß unter dem Walzdruck von 950°C heißen Stahlknüppeln, wodurch die Häufigkeit des Rollenwechsels drastisch reduziert wurde.
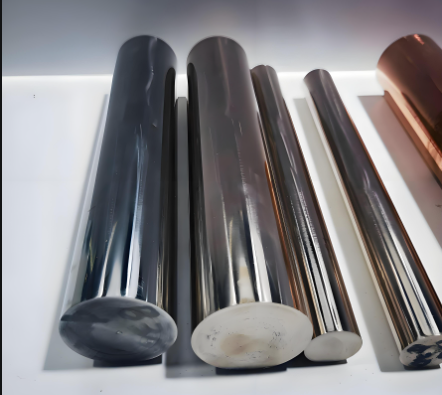
5. außergewöhnliche Verschleißfestigkeit. Die Verschleißfestigkeit der Legierung hängt eng mit ihrem WC-Gehalt zusammen. Bei der Verwendung von WC-Legierungen auf Nickelbasis für Kugelmühlenauskleidungen in Bergwerken, wo die Reibung beim Mahlen des Erzes sehr hoch ist, halten Auskleidungen mit dem WC-Gehalt 35% fünfmal länger als Standardstahlauskleidungen. In Zementproduktionsanlagen zeigen Verschleißbleche aus einer WC-Legierung auf Nickelbasis an Rohrbögen, die Zement transportieren, nach über einem Jahr nur minimalen Verschleiß, während Standardbleche in wenigen Monaten durchgescheuert sind. Oberflächenbehandlungen wie das Laserumschmelzen können die Verschleißfestigkeit weiter erhöhen; eine Maschinenfabrik hat die Lebensdauer von legierten Formen mit 30% nach dem Laserumschmelzen der Oberfläche erhöht.
6. die Korrosionsbeständigkeit variiert. WC-Legierungen auf Nickelbasis weisen je nach dem korrosiven Medium eine unterschiedliche Korrosionsbeständigkeit auf. In verdünnten schwefelsauren Lösungen weisen Legierungen mit höherem Mo-Gehalt eine bessere Korrosionsbeständigkeit auf. Einige Chemiewerke verwenden solche Legierungen für Rührflügel von Reaktionsgefäßen, die nach zwei Jahren in verdünnter Schwefelsäure nur eine geringe Oberflächenkorrosion aufweisen. In Meerwasser widerstehen Cr- und Mo-haltige Legierungen wirksam der Chloridionenkorrosion. Bauteile aus WC-Legierungen auf Nickelbasis auf Offshore-Ölplattformen behalten ihre gute Leistung auch bei langfristigem Eintauchen in Meerwasser und Scheuern und verhindern korrosionsbedingte Ausfälle.
7.Thermische Ausdehnung Koeffizient wirkt sich auf die Anwendung aus. Der Wärmeausdehnungskoeffizient (WAK) von WC-Legierungen auf Nickelbasis beträgt in der Regel (8 - 12) × 10-⁶/°C. Dieser Parameter ist für den Zusammenbau von Hochtemperaturgeräten von entscheidender Bedeutung. Beim Zusammenbau der Turbinenschaufeln von Flugzeugtriebwerken mit der Nabe muss der TEC-Wert der Werkstoffe übereinstimmen. Eine erhebliche Diskrepanz kann während der Temperaturzyklen beim An- und Abstellen des Triebwerks hohe thermische Spannungen erzeugen, die zu einer Lockerung oder zum Bruch der Schaufeln führen können. Bei der Konstruktion von Kompensatoren für Hochtemperaturrohre muss ebenfalls der TEC der Legierung berücksichtigt werden, um eine freie thermische Bewegung zu gewährleisten und Spannungsschäden zu vermeiden.
8. das Schweißen birgt Herausforderungen. Das Schweißen von WC-Legierungen auf Nickelbasis erfordert spezielle Verfahren. Aufgrund der hohen Härte und des hohen Schmelzpunkts von WC ist das Schweißen anfällig für Rissbildung und Porosität. Die Anwendung falscher Schweißmethoden bei der Reparatur von Bauteilen kann zu stark gerissenen Schweißnähten führen, was wiederum den Ausschuss von Teilen zur Folge hat. Richtiges Schweißen erfordert spezielle Elektroden und eine kontrollierte Schweißstromstärke und -geschwindigkeit. Ein Vorwärmen der Bauteile auf 200°C - 300°C vor dem Schweißen und ein langsames Abkühlen nach dem Schweißen sind unerlässlich, um thermische Spannungsrisse zu vermeiden.
Unser Unternehmen gehört zu den zehn führenden Unternehmen in China. Hersteller von Wolframkarbid. Sollten Sie Produkte aus Hartmetall benötigen, wenden Sie sich bitte an Kontaktieren Sie uns.