Schweissverfahren für Stanzwerkzeuge
Wolfram-Inertgas-Schweißen (WIG):
Prinzip: Das WIG-Schweißen ist eine Schweißtechnik, bei der Argongas als Schutzgas verwendet wird. Der Lichtbogen brennt unter dem Schutz von Argon, wodurch die Wärme konzentriert und die Oxidation der Schweißzone wirksam verhindert wird, wodurch qualitativ hochwertige Schweißnähte entstehen.
Anwendung: Wird häufig zum Schweißen von Stanzwerkzeugen aus Edelstahl, Aluminium und Aluminiumlegierungen verwendet. Es ist besonders effektiv für die Reparatur von Werkzeugen und die lokale Verstärkung. Beim Schweißen von Präzisions-Stanzwerkzeugen aus rostfreiem Stahl beispielsweise gewährleistet das WIG-Schweißen glatte und saubere Schweißnähte und minimiert die Auswirkungen auf die Oberflächenqualität des Werkzeugs.
Merkmale: Beim WIG-Schweißen entstehen qualitativ hochwertige Schweißnähte mit einer ästhetisch ansprechenden Nahtbildung, einer kleinen Wärmeeinflusszone und einer relativ geringen Verformung. Es erfordert jedoch ein höheres Maß an handwerklichem Geschick und ist mit relativ hohen Gerätekosten verbunden.
Widerstandsschweißen:
Das Prinzip: Beim Widerstandsschweißen wird die Widerstandswärme, die beim Stromdurchgang durch die Werkstücke entsteht, genutzt, um diese lokal in einen plastischen oder geschmolzenen Zustand zu versetzen und so eine feste Verbindung unter Druck herzustellen.
Anwendung: Geeignet für das Schweißen von dünneren Stanzformkomponenten, z. B. Punktschweißen oder Nahtschweißen von Blechstanzformen. Bei der Herstellung von Stanzwerkzeugen für die Automobilindustrie wird das Widerstandsschweißen häufig zum Schweißen von Karosserieteilen verwendet.
Merkmale: Schnelle Schweißgeschwindigkeit, hohe Produktionseffizienz, minimale Schweißverformung und kein Bedarf an Zusatzwerkstoffen. Allerdings sind die Ausrüstungskosten hoch, und die Anforderungen an die Oberflächenqualität und die Montagegenauigkeit der Werkstücke sind streng.
Laserschweißen:
Das Prinzip: Beim Laserschweißen wird ein Laserstrahl mit hoher Energiedichte als Wärmequelle eingesetzt, um das Oberflächenmaterial des Werkstücks schnell zu schmelzen und zu verfestigen, so dass eine Schweißverbindung entsteht. Der Laserstrahl bündelt die Energie und ermöglicht so ein schnelles Schweißen.
Anwendung: Besonders geeignet für Präzisionsstanzwerkzeuge, wie z. B. mikroelektronische Stanzwerkzeuge und Präzisionsstanzwerkzeuge für Hardware. Bei dünnen und empfindlichen Stanzwerkzeugen werden mit dem Laserschweißen hochwertige Schweißnähte mit minimaler thermischer Belastung erzielt.
Merkmale: Hohe Schweißpräzision, schmale und tiefe Schweißnähte, eine kleine Wärmeeinflusszone und extrem geringe Verformung. Das Verfahren ermöglicht auch automatisiertes Schweißen. Allerdings sind die Kosten für Ausrüstung und Wartung hoch und die Anforderungen an den Bediener sind hoch.
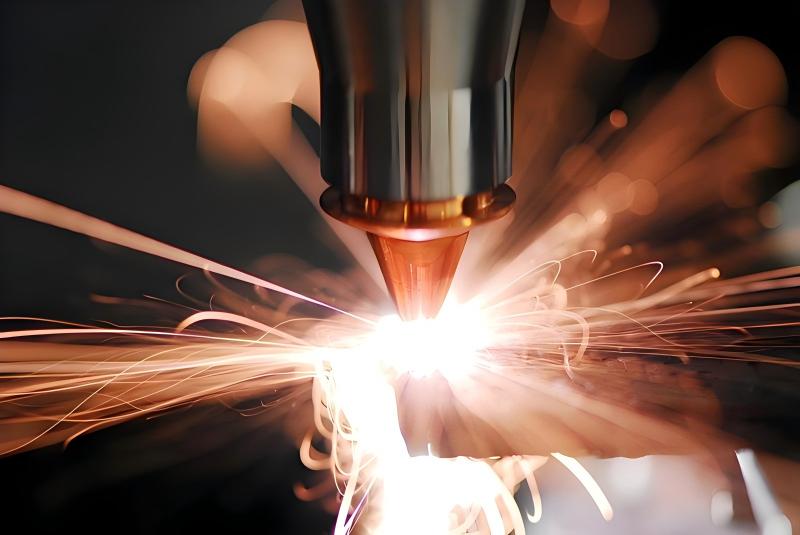
Metall-Schutzgasschweißen (SMAW):
Prinzip: Beim Stumpfschweißen wird die zwischen der Elektrode und dem Werkstück erzeugte Lichtbogenwärme genutzt, um Elektrode und Werkstück lokal zu schmelzen und eine Schweißnaht zu bilden. Während des Betriebs fungiert die Elektrode als Zusatzwerkstoff, der unter der Lichtbogenhitze schmilzt und die Schweißnaht füllt.
Anwendung: Geeignet zum Schweißen und Reparieren großer Stanzwerkzeuge. Es bietet eine hohe Anpassungsfähigkeit an die Schweißpositionen und ermöglicht das Schweißen in verschiedenen räumlichen Ausrichtungen. Für strukturell einfache Werkzeuge mit geringeren Präzisionsanforderungen ist das Stumpfschweißen ein gängiges Schweißverfahren.
Merkmale: Einfache Ausrüstung, flexibler Betrieb und niedrige Kosten. Die Qualität der Schweißnaht hängt jedoch stark von den Fähigkeiten des Bedieners ab, der Arbeitsaufwand ist hoch, die Effizienz ist relativ gering, und die Qualität und das Aussehen der Schweißnaht sind schlechter als beim WIG- oder Laserschweißen.
Unterpulverschweißen (SAW):
Prinzip: Das UP-Schweißen ist ein Schweißverfahren, bei dem der Lichtbogen unter einer Flussmittelschicht brennt. Während des Schweißens bedeckt das Flussmittel die Schweißzone, und der Lichtbogen erzeugt unter der Flussmittelschicht Wärme, die den Draht und das Werkstück zum Schmelzen bringt und die Schweißnaht bildet.
Anwendung: Geeignet für das Schweißen dickerer Stanzformkomponenten, wie z. B. Böden oder Rahmen großer Stanzformen. Im Schwermaschinenbau wird SAW häufig zum Schweißen großer Stanzwerkzeuge verwendet.
Merkmale: Hoher Schweißstrom, tiefer Einbrand, hohe Schweißgeschwindigkeit, hohe Produktionsleistung und stabile Schweißqualität. Die Ausrüstung ist jedoch komplex, die Anforderungen an die Präzision der Werkstückmontage sind hoch, und es ist ungeeignet für dünne Bleche oder komplexe räumliche Schweißnähte.
Hartlöten:
Prinzip: Beim Hartlöten wird ein Zusatzwerkstoff (Lot) mit einem niedrigeren Schmelzpunkt als der des Grundmetalls verwendet. Das Werkstück und der Lotwerkstoff werden auf eine Temperatur über dem Schmelzpunkt des Lotwerkstoffs, aber unter dem Schmelzpunkt des Grundmetalls erhitzt. Der geschmolzene Zusatzwerkstoff benetzt das Grundmetall, füllt den Fugenspalt und diffundiert mit dem Grundmetall, um eine Verbindung zu bilden.
Anwendung: Häufig verwendet für HartmetallKeramik und Metalle sowie das Schweißen temperaturempfindlicher Werkzeugkomponenten. Bei Stanzwerkzeugen aus Hartlegierungen können zum Beispiel Hartlegierungsblätter durch Hartlöten mit dem Werkzeugkörper verbunden werden.
Eigenschaften: Das Grundmetall schmilzt beim Löten nicht, was zu einer minimalen Verformung der Verbindung führt und die Maßgenauigkeit erhält. Allerdings haben Hartlötverbindungen eine relativ geringere Festigkeit, und die Wahl des Schweißzusatzes hat erhebliche Auswirkungen auf die Schweißqualität.
In der Praxis sollte das geeignete Schweißverfahren auf der Grundlage von Faktoren wie Material, Struktur, Nutzungsanforderungen und Produktionsvolumen des Stanzwerkzeugs ausgewählt werden. Um die Qualität des Schweißens zu gewährleisten, müssen außerdem die Schweißprozessparameter richtig eingestellt und kontrolliert werden, und nach dem Schweißen sollten je nach Bedarf eine Wärmebehandlung und eine Bearbeitung durchgeführt werden.
Unser Unternehmen gehört zu den zehn führenden Unternehmen in China. Sinterkarbid-Hersteller. Sollten Sie Produkte aus Hartmetall benötigen, wenden Sie sich bitte an Kontaktieren Sie uns.