Parameters of Nickel-based Tungsten Carbide Alloy
1.Chemical Composition Determines Fundamental Properties. In nickel-based WC alloys, nickel acts as the base element, typically constituting 60% – 85% of the composition. In some customized aerospace alloy components, the nickel content reaches 75%, imparting excellent toughness and corrosion resistance. Tungsten carbide (WC) is the key strengthening phase, generally present at 15% – 40%. For wear plates in mining machinery alloy parts, a WC content of 30% significantly increases surface hardness. Besides nickel and WC, elements like chromium (Cr), molybdenum (Mo), and niobium (Nb) are often added. Chromium enhances oxidation resistance; for example, alloy cutting tools operating in high-temperature environments contain 5% – 15% Cr, effectively preventing surface oxidation. Molybdenum enhances high-temperature strength; in aero-engine components, its addition allows the alloy to maintain good strength even at 800°C.
2.Significant Variation in Hardness Indicators. The hardness of nickel-based WC alloys varies considerably depending on processing techniques and applications. Alloys prepared by powder metallurgy and sintered can achieve hardness levels of HRC 60 – 70. In automotive parts factories, molds produced this way withstand tens of thousands of metal stamping cycles without significant wear. Overlay welding (hardfacing) typically yields alloy layers with hardness around HV 800 – 1200. Applying nickel-based WC alloy via overlay welding to the lip edges of port crane grabs significantly improves wear resistance. Grabs that previously required replacement every six months can last up to two years after hardfacing.
3.Relatively Stable Density Values. The density of nickel-based WC alloys typically ranges from 10 – 12 g/cm³. This density is crucial when casting alloy parts. For instance, a foundry producing large alloy bearing seats experienced significant weight deviations in cast parts due to alloy composition fluctuations affecting density. Normally, higher nickel content and lower WC content result in lower density, while higher WC content increases density. Strict density control is essential for precision instrument alloy components to ensure weight meets design specifications.
4.Outstanding High-Temperature Performance. Nickel-based WC alloys exhibit exceptional performance in high-temperature environments. Their typical operating temperature range is 600°C – 1000°C. In boiler pipe weld repairs for thermal power plants, using nickel-based WC alloy welding rods allows the pipes to maintain good wear resistance and strength under the scouring action of 850°C high-temperature steam. At 900°C, the alloy’s tensile strength can still exceed 500 MPa. For example, the surface of a steel mill’s reheating furnace roller table, coated with nickel-based WC alloy, showed minimal wear under the rolling pressure of 950°C steel billets, drastically reducing roller replacement frequency.
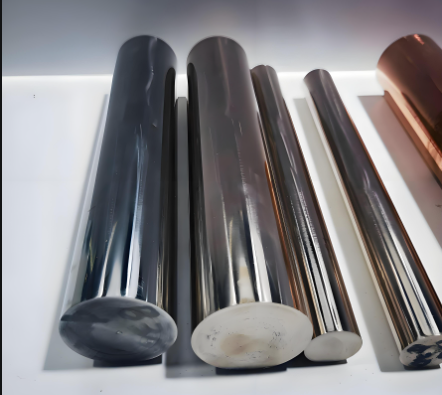
5.Exceptional Wear Resistance. The wear resistance of the alloy is closely related to its WC content. Using nickel-based WC alloy for ball mill liners in mines, where friction during ore grinding is intense, liners with 35% WC content last 5 times longer than standard steel liners. On cement production lines, using nickel-based WC alloy wear plates at pipe elbows transporting cement shows minimal wear after over a year, whereas standard plates wear through in months. Surface treatments like laser remelting can further enhance wear resistance; one machinery factory increased the wear life of alloy molds by 30% after laser remelting the surface.
6.Corrosion Resistance Varies. Nickel-based WC alloys exhibit different corrosion resistance depending on the corrosive medium. In dilute sulfuric acid solutions, alloys with higher Mo content demonstrate better corrosion resistance. Some chemical plants use such alloys for reaction vessel agitator blades, showing only slight surface corrosion after two years in dilute sulfuric acid. In seawater environments, alloys containing Cr and Mo effectively resist chloride ion corrosion. Components made from nickel-based WC alloy on offshore oil platform equipment maintain good performance despite long-term seawater immersion and scouring, preventing corrosion-induced failures.
7.Thermal Expansion Coefficient Impacts Application. The thermal expansion coefficient (TEC) of nickel-based WC alloys is typically (8 – 12) × 10⁻⁶/°C. This parameter is vital for assembling high-temperature equipment. For instance, when assembling aero-engine turbine blades to the disk hub, the TEC of the materials must match. A significant mismatch can generate high thermal stresses during engine start-up/shutdown temperature cycles, potentially causing blade loosening or fracture. Designing expansion joints for high-temperature pipes also requires considering the alloy’s TEC to ensure free thermal movement and prevent stress damage.
8.Welding Presents Challenges. Welding nickel-based WC alloys requires specialized processes. Due to the high hardness and melting point of WC, welding is prone to cracking and porosity. Using incorrect welding methods during component repair can result in heavily cracked welds, leading to part rejection. Proper welding necessitates specialized electrodes and controlled welding current and speed. Preheating components to 200°C – 300°C before welding and implementing slow cooling post-weld are essential to prevent thermal stress cracking.
Our company is among China’s top ten tungsten carbide manufacturers. Should you require cemented carbide products, please contact us.