4 Key Differences Between Tungsten Carbide VS HSS High-Speed Steel
Tungsten carbide vs HSS: Tungsten carbide (often referred to as “carbide steel”) and high-speed steel (HSS) are frequently compared in industrial applications, yet they exhibit fundamental differences in composition, performance, and application scenarios. Material selection directly impacts product lifespan and production costs, and understanding these distinctions enables engineers to make informed decisions for critical components such as cutting tools and molds.
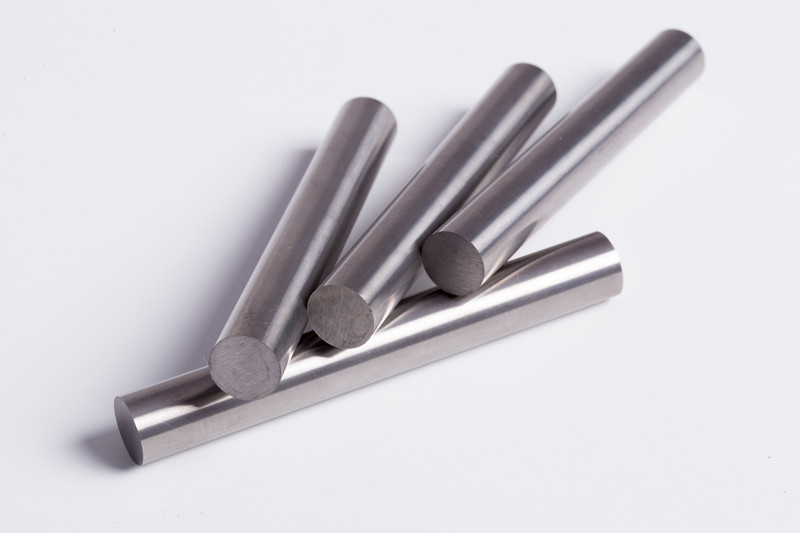
1. Inherent Compositional Differences Dictate Performance
Tungsten carbide is a cemented carbide composed of over 90% tungsten powder bonded with a cobalt matrix through high-temperature sintering. This structure resembles the reinforcement of steel bars in concrete, where the cobalt binder (typically 6–12% by weight) acts as the “cement.” A 1% variation in cobalt content alters the transverse rupture strength by approximately 200 MPa, enabling precise balancing of hardness and toughness.
In contrast, high-speed steel is a high-carbon alloy steel containing 5–20% tungsten, formed via smelting to create a homogeneous structure. Its properties rely on solid-solution strengthening effects from alloying elements like chromium, vanadium, and molybdenum. This compositional divergence results in distinct microstructures: tungsten carbide exhibits densely packed polyhedral WC grains, while HSS features a martensitic matrix with dispersed carbides.
2. Hardness and Heat Resistance: Polarized Performance
Tungsten carbide achieves a room-temperature hardness of HRA 89–94 (equivalent to HRC 70+), retaining sharpness even when machining titanium alloys. At 800°C, its hardness decreases by only ~10%, owing to WC’s exceptional thermal stability.
High-speed steel, with a hardness range of HRC 63–67, undergoes significant softening at 600°C despite surface coatings (e.g., TiN or AlCrN). A case study in automotive transmission gear machining revealed that carbide tools tripled productivity compared to HSS, albeit with 5× higher initial costs.
3. Manufacturing Costs: Diverging Economic Curves
Producing tungsten carbide via powder metallurgy requires sintering temperatures exceeding 1,400°C, with energy consumption of ~3,500 kWh per ton. Cobalt price volatility further impacts material costs. Carbide inserts are typically brazed or mechanically clamped, offering high scrap recovery value.
HSS, manufactured through electric arc furnace smelting at ~600 kWh per ton, allows plastic deformation via forging or rolling. A tooling factory reported that HSS drill bits can be reground 15 times, whereas carbide tools are often single-use. This creates complementary cost profiles: HSS favors maintenance flexibility, while carbide prioritizes longevity.
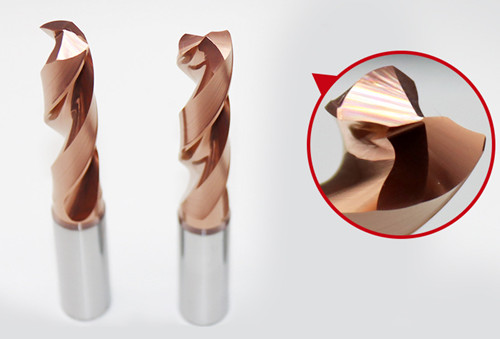
4. Application Scenarios: Balancing Economics and Performance
Tungsten carbide dominates CNC machining centers, achieving cutting speeds of 250 m/min for cast iron—5× faster than HSS. However, in intermittent cutting (e.g., machining shafts with keyways), HSS’s impact resistance excels. A comparative study in aircraft manufacturing showed HSS tools reduced chatter by 40% and improved surface finish when machining aluminum thin-wall components.
This performance dichotomy stems from intrinsic material properties: HSS’s elastic modulus (~250 GPa) provides vibration damping, while carbide’s rigidity (~600 GPa) sacrifices vibration attenuation for stability.
Strategic Selection: A Multidimensional Approach
Engineers must evaluate lifecycle costs rather than upfront expenses. A mold manufacturer switching to carbide punches saw 80% higher unit costs but 6× extended tool life, yielding a 35% total cost reduction. For low-volume production, HSS’s regrindability often proves more economical.
Future advancements, such as 3D printing of complex carbide geometries, may disrupt traditional cost paradigms, reshaping competition in the cutting tool industry. By integrating material science with operational economics, engineers can optimize performance and profitability across diverse industrial applications.